導入事例
オフコン時代から「UP-One」を利用し、3代目のリプレース。業務を見直し従来の課題を解決。正しい在庫数を把握できるようになり、対外的な信用力も向上しました。
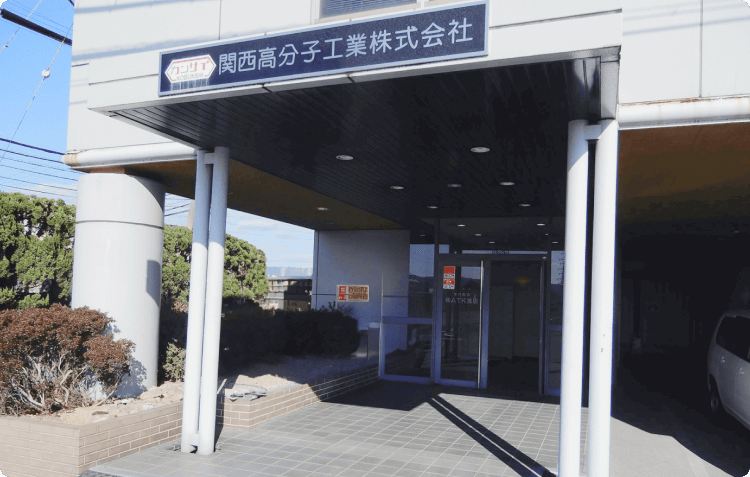
関西高分子工業株式会社
代表取締役社長 池田 祐司 様、営業部 営業課 主任 大塚 正樹 様
ポリエチレンフィルム製造・加工・販売を手掛ける関西高分子工業株式会社は、2012年、それまで10年以上使い続けてきた「UP-One」のリプレースを行いました。リプレースプロジェクトについての話を中心に、その一世代前のオフコン版から長年利用を続けている理由などを、池田社長と営業部の大塚主任に伺いました。
この記事のポイント!
課題
-
世の中の品質基準の向上に伴い、要求に対応できるシステムが必要になった
-
在庫管理が厳密にはできていなかった
導入スケジュール
- 2012年3月~2013年2月(約11ヵ月)
導入効果
-
「UP-One」で必要な資料が出力可能となり、対外的な質問への回答スピード・内容の信頼度が向上
-
正しい在庫数量の把握
関西高分子工業株式会社について
―1935年(昭和10年)創業ということで、歴史ある貴社について教えていただけますか?
以下、年表に沿ってご紹介します。
1935年 |
大阪府布施市(現在の東大阪市)に宇野清工舎創立 セルロイド製の美容器具を作っていました。 資料は残っていないのですが、戦前に美容器具があったのですね。 |
---|---|
1961年 |
宇野高分子工業株式会社に社名変更 この頃、ポリエチレンやポリプロピレンなどいわゆる「高分子」が日本で作られるようになり、当社もポリプロピレンを扱っていたので社名に「高分子」をつけました。高分子製品製造のさきがけとなった企業でした。 この頃は、ポリプロピレン製の食器を作っていました。 |
1967年 |
ポリエチレンチューブの生産開始 食器製造からポリエチレンチューブ生産に移管しました。この年、親会社の稲畑産業株式会社(以下、稲畑産業)が資本参加しています。 |
1969年 |
関西高分子工業株式会社に社名変更 この年、宇部興産株式会社(以下、宇部興産)が資本参加。宇部興産とは、資本参加前から原料の取引をしていたので、稲畑産業含め、長い付き合いになります。 後述のAPPLE FILM設立の際にも、出資していただきました。 |
1990年 |
タイにAPPLE FILM CO.,LTD設立
ちなみに社名の「APPLE FILM」、候補をことごとくタイ国から却下され、当時タイでは貴重であった「りんご」に落ち着きました。アルファベットで書くと「A」で始まり、企業リスト等では最初に出てくるので良いと思いました。 |
1993年 | 本社を現在の奈良県大和郡山市に移転 |
―オフコンの時代から「UP-One」を使われているそうですね。
はい、30年近く前になりますが、株主である宇部興産からの紹介で導入しました。
何をどうしたらいいか右も左も分からない、そういう時に一番頼りやすいのは親会社ですからね。系列会社で、信頼のおけるシステム会社がないか探していた時に、宇部情報システムさんの名前が挙がりました。前述の通り、宇部興産とは資本参加以前から付き合いがありましたから、信頼する会社の紹介ということもあり安心してスタートが切れました。
―貴社に「UP-One」を見学に来た企業様が導入を決められたとお聞きしましたが。
はい、当社に見学に来て、導入を決められた同業者がいます。お役に立てて嬉しいです。2018年にタブレット機能を追加されたとある企業も、うちに何度も見に来られ、現在は当社と同じようにタブレットを使用しているようです。当社も、うまく運用できているので、他社に胸を張って紹介ができます。
2012年「UP-One」リプレース
―リプレースを検討された理由をお聞かせください。
リプレースを検討した1番の理由は、今後、求められるものに応じていかないとこの業界では生き残れないと判断し、要求に対応できるシステムの必要性を感じたからです。
世の中の品質基準が上がり、ISOなどの影響もあり、対外的な報告・資料の提出が必須になってきました。管理体制、使用している基幹システムなど、また、その裏付けの提示も求められるようになりました。聞かれた時にすぐ答えられる、そして相手に理解してもらいやすいシステムに変えていかないといけないと思いました。同じ「UP-One」というシステムのリプレースですが、ただの焼き直しではありません。業務を見直し、今ある課題は解決する…結構な大改革でした。私たちにとって、在庫は資産です。在庫がいまどこにどの状況であるのか、逐一追跡できる、いろいろな帳票が出せて、出荷の時にはスキャナーで読み取ればチェックもできる、というシステムが必要でした。
―他のシステムは検討されなかったのですか?
フィルム製造の業種に合うシステムって、まずありません。その上「UP-One」は、さらにニッチで絶対他に真似できないシステムにバージョンアップされていたので、他システムを検討する余地なんてありませんでした。他に候補がないのです。他のシステム会社から営業の電話はよくかかってきます。説明は一応聞きますが、うちの業務をカバーすることは無理なので断っています。他のシステムに代わりはできません。
―スケジュールについて教えてください。
以下、表の通りです。
2012年4月~7月 (約4ヵ月) |
カスタマイズのためのヒアリング(3回)、レビュー(1回) |
---|---|
2012年12月、2013年2月 (約2ヵ月) |
データ移行 |
2012年12月~2013年1月 (約2ヵ月) |
総合テスト |
2013年1月 (約1ヵ月) |
追加カスタマイズ、結合テスト |
2013年2月 | 本番稼働 |
―カスタマイズのメインとなったタブレット機能についてお聞かせください。
当社はリプレースの際に、カスタマイズし、タブレット機能を追加しました。タブレットは製造実績の入力と倉庫の受払管理で利用しており、合計9台導入しています。「UP-One」リプレースにおいて1番のテーマであったのが、「正の在庫を把握する」ということでした。それまでは棚卸の際、人が目で見て、紙に管理No.・サイズ・数量を書き、さらにそれをExcel®に転記していました。人がやることなので数え間違い、見間違い、書き間違い、間違える要素はたくさんありました。間違えたまま翌月になり、さらに翌月になり…桁を間違えた日には一大事です。タブレットは、価格も安く、画面の情報量も多く見やすい、持ち運びもしやすい、入力もタッチでできるので採用しました。
―苦労されたことはありましたか?
上位管理者と現場作業員との妥協点を見つけることに苦労しました。
管理者の「ここまでは絶対にやってほしい」、現場の「そこまではできない」のせめぎ合いでした。新システムの運用を、日々の業務に理論上詰め込むことは簡単です。しかし、それをリアルに現場でできるかというと、できることとできないことがあります。手間だけが増える、今の要員数では限界が来る、限度を見極めながら、「ここまではやろう」「これは代わりにこうしよう」と1つ1つ調整や摺り合わせを実施しました。例えば本来なら、外部委託した加工品が戻ってくる、それに付いている伝票のQRコードをリーダーで読み取り、現物を確認してタブレットに数量を入力するのが理想です。しかし実際は、1件1件見ていられないので、先に倉庫に入庫し、QRコード読み取り・数量入力を後でまとめて行っています。
また、当初は、製造現場、仮置き場、自動倉庫、それ以外など、倉庫を区分で細かく分ける予定にしていました。しかし、各所に仕掛品や製品などが置かれている工場内で、区間移動のたびにタブレット入力はできないと、物流部門からの大反対を受け、製造現場とそれ以外の2つの区分に分けることにしました。タブレットの操作に関しても、若い人はスマートフォンで慣れているでしょうけど、多くの作業員には「こんなの1回1回入力しないといけないのか」と、初めはなかなか受け入れてもらえませんでした。
リプレース後1年くらいは少し混乱しましたが、今は問題なく運用できています。
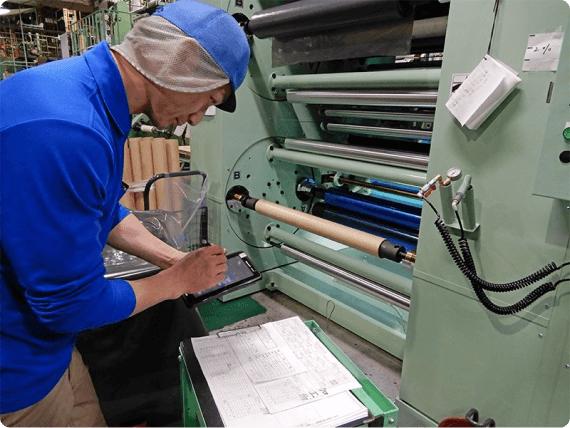
タブレット使用風景
「UP-One」の導入効果
―業務を見直してリプレースを実施した、効果はいかがでしたか?
このリプレースで、当社のシステム運用は刷新されたと言っても言い過ぎではありません。
当社の業務の根幹部分が対応できるように一気に刷新しました。それまでも「UP-One」は利用していましたが、実は業務と直結していませんでした。対外的に、「UP-One」を使っていますと説明するような使い方ができていませんでした。
例えば、原反に管理No.を設定し、それが製品になるまで、いろいろな工程を通ります。そのトレーサビリティが、厳密に言うとできていませんでした。管理No.で検索したら、いつどの機械で原反を作り、どの加工業者に委託して…等の情報は分かりますが、厳密にはリンクされていなかったのが実情です。
そして1番の効果は、在庫の正ができたことです。正しい在庫が何なのか分かるようになりました。リプレース後は「UP-One」の在庫を正とし、管理するようにしました。棚卸の際は実棚の数を管理No.単位に「UP-One」に入力し、「UP-One」上の在庫数と比較できます。今は「UP-One」に標準で搭載されている以下の帳票が便利で、棚卸も楽になりました。
【「UP-One」帳票】
ゼロ補正差異表
「UP-One」にはあるが実棚にはない在庫を管理No.単位にリスト化した帳票。
棚卸差異表
「UP-One」の在庫数と実棚数が違うデータが出力される帳票。
正の在庫が把握できているのといないのでは、対外的に説明する場合に、スピードも相手への信頼度も違います。説得力のある管理方法になりました。
―アフターサポートについてはいかがですか?
大変なこともありましたが、困ったときは担当のSEさんが協力してくださいました。そのフォロー体制にも救われました。リプレース後当初は、何かあればしょっちゅうお電話していました。だいたいのことはすぐ解決しました。ことこまかく訪問もしてくださいました。最近は、私たちもシステムを熟知してきているので、電話で事足りるため、なかなかお呼びする機会がなくてさみしいです(笑)。
運用サポートがすばらしい、そこが1番。当社は当たりの担当者を引いたと思います。
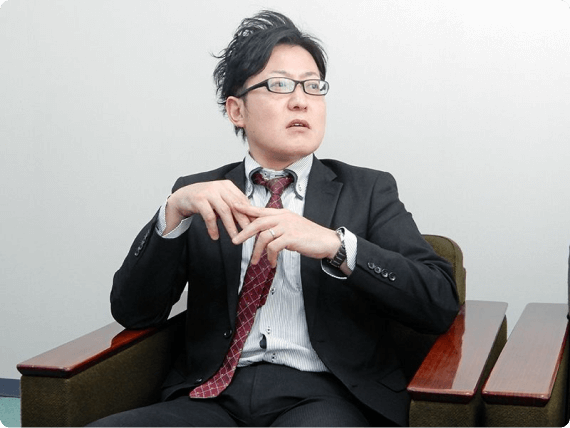
在庫=資産。正しい在庫数を把握できるようになったことが1番の効果です。
(大塚主任)
宇部情報システムへの評価
―宇部情報システムの総評をお聞かせいただけますか?
私たちも知らない昔から、30年近くも長きにわたり、大変お世話になっています。ずっと「UP-One」を使い続けている理由の1つは、システムの品質、他にない機能、そして、担当者の対応のすばらしさだと思います。要所要所で良いアドバイスをくださって、それに従っていけば最終的に解決すると認識しています。この業界に「UP-One」をどんどん広めていきたいです。そのお手伝いができるなら、協力させてください。この記事をいくらでも他社様に紹介してください。今後もよろしくお願いいたします。
関西高分子工業株式会社
ポリエチレンフィルム製造・加工・販売
創業は昭和10年。セルロイド製品・ポリプロピレン製品の生産を経て、現在は、産業分野から食品分野まで多岐に渡るポリエチレンチューブ及びフィルムの製造・販売を行っている。日本の高分子製品製造の先駆者であり、業界のグローバル化に対応すべく、1990年にはポリエチレン製造の企業としては初の海外進出を果たしている。環境に優しいクリーンな生産環境で、安心して使用できる商品作りを心がけ、絶えずお客様に満足していただくことを第一に考えている。
- 創業
- 1935年
- 本社
- 奈良
データの一元管理で
ムダ・ミス解消
経営判断を効率よくスマートに