コラム
非破壊検査とは?メリット・デメリット、製造現場での活用法を紹介
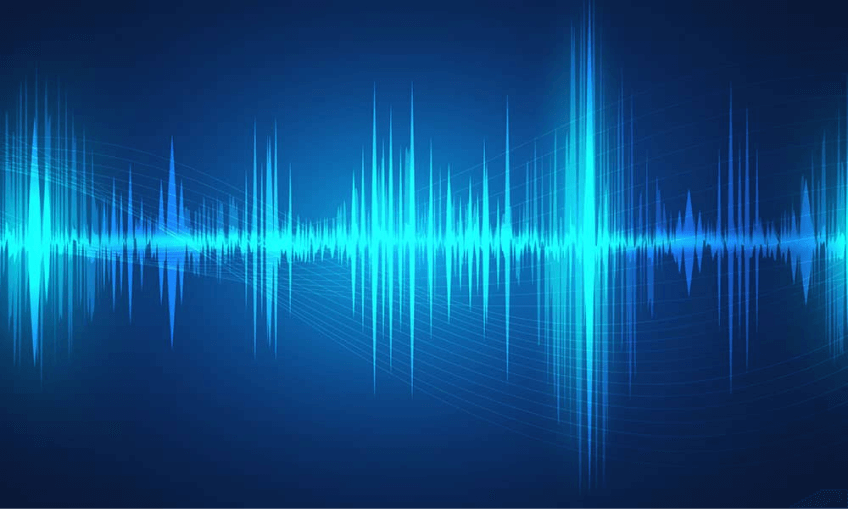
非破壊検査とは、検査対象物を損壊することなく内部の良品・不良品を判定する検査方法のことです。製造業の検査の手法として広く採用されています。非破壊検査にはさまざまな種類があり、検査方法によって適性が異なるため、検査対象の製品や検査項目によって最適な手法を選択する必要があります。
本記事では、非破壊検査の各手法とUISの超音波探傷システムについて解説していきます。
1. 非破壊検査とは
非破壊検査とはどんな検査方法なのか、目的や役割を解説します。対象物を傷つけることなく検査をおこなえることが特徴ですが、材質や形状によって利用できる手法が異なります。
モノを壊さず状態や品質を調べる検査技術
非破壊検査は文字通り、検査対象物を壊さずに欠陥や劣化の状況を調べる検査技術のことです。建物、橋、鉄道など大きなものから、車や家電などのあらゆる物が検査の対象となります。検査対象を傷つけない超音波や放射線などを利用します。
破壊検査と非破壊検査の違い
非破壊検査と対になる検査が「破壊検査」です。製品や部品の内部欠陥を調べるために、切断もしくはそれに準じた方法で内部の状態を確認します。このように検査対象物を破壊するか、あるいは、対象物の機能や価値が損なわれるような扱い方で検査する方法を破壊検査と呼びます。
これに対し非破壊検査は、前述したように検査対象物を壊すことなく、製品・部品の価値を損なわずに内部の状態を検査することが可能です。
また、破壊検査と非破壊検査の中間的なものとして扱われる検査方法に「部分破壊検査」があります。この方法は検査対象物の形をわずかに変形させるものの、製品・部品が有する機能や特性には影響を及ぼしません。部分破壊検査の代表的な種類としては、硬さ試験や材質判定を行うための火花試験などが挙げられます。また、材料試験は破壊検査の一種として捉えられることが多いものの、部分検査に属する検査(試験)であるという見方もあります。
製造業における非破壊検査の目的
ビルや橋など構造物に対する非破壊検査は、劣化の状況を確認し、予防保全を目的として実施されます。一方で、製造業では品質検査や寿命評価を目的に非破壊検査がおこなわれます。
品質検査とは、製造物が規定の基準に適合しているか評価することです。品質検査によって、不具合の有無を確認し、製品の信頼性を担保します。非破壊検査では製造物を傷つけないため、完成品を無駄にすることがなく、全数検査も可能になります。
2. 非破壊検査の方法
非破壊検査にはさまざまな手法があり、目的に応じて最適な検査手法を選択します。製造業の品質検査に活用する場合は、検査対象物と検査項目に合ったものを選ぶ必要があります。超音波や放射線、レーダーなど一般的に利用されている手法を5つ紹介します。
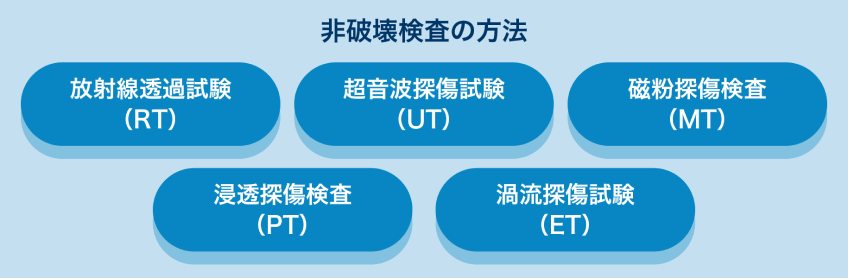
放射線透過試験(RT)
放射線透過試験はX線を利用し、内部の傷の検出や厚さの測定に利用されます。X線を検査対象物に透過させ、透過した放射線の強さの変化を測定し傷の有無を調べます。X線で撮影するため、内部の状態を画像化したものをモニタで確認することができます。
表面から深層部の傷まで検出できるため、体積のある製品の検査にも適しています。非破壊検査の中でも広く普及している検査方法であり、幅広い検査対象物に対応できる特徴を持った手法です。
超音波探傷試験(UT)
超音波を利用した検査方法で、放射線透過試験と同様に内部の傷の検出や厚さの測定に利用できます。超音波は波長が短いほど直進性があり、物質の境界面で反射されやすい性質を持っています。放射線と比べて安全性が高いため、広く使用されている方法の一つですが、複雑な構造を持つ物体の検査には不向きです。
磁粉探傷検査(MT)
鉄鋼材料などの強磁性体の表面、または表面直下の傷検出に利用される検査方法です。高感度かつ検査工程も少ないメリットがあるものの、鉄粉を散布し傷を発見するため、非磁性体に利用することはできません。
浸透探傷検査(PT)
浸透性のよい検査液を検査対象物に浸透させ、表面の傷や割れ、プロホールなどを検出する検査方法です。木材などを除き、ほとんどすべての金属・非金属で利用できるため広く利用されていますが、検査工程が多い欠点もあります。
渦流探傷試験(ET)
表面の傷の検出や膜厚の測定、材料の判別に利用される検査方法です。高速の試験が可能であり、前処理・後処理不要で電気信号処理のみで判定ができるため、製造ラインでの検査に適しており、広く採用されています。
3. 非破壊検査のメリット
製造業の品質検査に、超音波や放射線を用いた非破壊検査を導入するとさまざまなメリットが生まれます。従来の目視検査との比較も含め紹介します。
検査のためのロスが発生しない
非破壊検査は製品を損傷することがないため、完成品を無駄にすることがありません。また、製品についてクレームが発生した際に故障の要因を調査する場合も役立ちます。
目視検査と比較し精度が高い
内部の異常を目視検査するため、対象物を切断するなど目視できる形に加工(破壊)する必要がありますが、目視判定可能な形に切断する加工技術の困難さに加え、熟練の検査員と新人検査員との技術・経験の差、本人の疲労や体調による基準のブレ、ヒューマンエラーによる見落としなどの課題が挙げられます。検査基準が一定でないと、品質のムラにつながってしまうのです。一定基準で迅速に品質検査を実施したい場合は、超音波などを使った手法が適しています。
また、非破壊検査により取得された情報は検査結果をデータとして残すことが可能です。データを製造部門にフィードバックすることで、品質に影響を与える製造プロセスの見直しや改善に役立てることができ、製品の質向上や不良率の低下に貢献します。
検査の自動化や全数検査が可能
非破壊検査は手法によって、全自動・半自動での検査が可能になります。破壊検査や目視検査の場合は人による作業が必要になり、属人的な部分を排除できません。製造ラインに組み込むことができる手法を採用すれば、検査のためのプロセスを加える必要がなく、効率よく製造・検査・納品まで進行することが可能になります。
4. 非破壊検査のデメリット
非破壊検査による自動化を進めるにあたって、デメリットも事前に把握しておく必要があります。注意しておきたい点を3つ紹介します。
適用可能な物質や形状が限られる
非破壊検査は手法ごとに得意・不得意な項目や利用できない材料があります。検査手法の特性を熟知した上で、検査項目や対象物の材質、形状などを考慮して手法を選ばなくてはいけません。
検出できない欠陥がある
X線や超音波などを利用し内部の欠陥を発見する非破壊検査は万能ではありません。内部のデータが取得できたとしても、欠陥を必ずしも見つけられるとは限らず、破壊検査と比較すると不確実性な部分があります。事前に発生しうる欠陥や場所などを予想できる知識や経験が必要です。
水没させる必要がある
超音波を利用した非破壊検査をおこなうためには、検査対象物を水中に浸す必要があります。
5. UISの非破壊検査「超音波検査」
宇部情報システムが提供する非破壊検査は、超音波技術を用いた「超音波検査」を採用しています。
超音波による検査は放射線(X線)透過による検査と同様、一般的に広く普及している非破壊検査の一手法です。超音波はX線のように免許・届出が不要のため、X線と比較し導入ハードルが低い検査手法と言えます。
超音波探傷検査の仕組み
超音波画像を得るために探触子といわれるセンサーを動かします。この探触子の内部には超音波の発生、受信を行う機能が組み込まれています。探触子から発する超音波を対象物に当てると音波は対象物の内部を伝搬し、キズ等による物質変化が無い場合、超音波は底面で反射し(エコー)再び戻ってきます。途中に物質変化があると底面より先にエコーが探触子に戻ってきます。
UIS超音波探傷システムの特長
宇部情報システムの「超音波探傷システム(SAT)」は、水没させた検査品に探触子を動かし超音波で画像化、画像処理技術を用いて欠陥を検出します。
取得した画像データを基にシステムが自動で正常・不良判定を行うため、全数検査の実現にも向いています。また、一本の探触子で取得できる画像データはスポット的な個所に限られてしまうのが一般的ですが、UISのシステムでは探触子を同時に複数動かすことで、面によるスキャンでの検査を実現しています。
宇部情報システムは超音波検査で全数検査を実現するトータルシステムをご提案いたします。非破壊検査の導入・自動化、現在の方法から見直しを検討されている企業様は、ぜひ当社へご相談ください。
製品の品質安定・向上によるブランディング強化
画像処理検査URCPをさらに知りたい方はこちら
URCPについてのご質問やご相談など、お気軽にお問い合わせください。