コラム
スマートファクトリーの事例3選をご紹介!メリットや注意点も解説

スマートファクトリーとは端的に言うと、AIやIoT技術を活用した工場のことです。生産性の向上をはじめ多くのメリットがあるため、多くの製造現場がスマートファクトリーの実現を目指しています。
本記事では、スマートファクトリーの定義やメリットに加えて、スマートファクトリーを実践している企業の事例をご紹介します。併せて、推進時の注意点も解説するため、成功の秘訣を理解できるでしょう。
スマートファクトリーの実現を検討している方は、ぜひ最後までお読みください。
目次
1. スマートファクトリーとは?
スマートファクトリーとは、生産性・品質の向上を目的に、AIやIoT技術を活用する工場を指します。
工場内の設備や機器をネットワークで繋ぎ稼働データ等を収集。分析結果を課題解決に役立てることが特徴の一つです。
スマートファクトリーは製造現場の生産性や品質問題を解決するものとして、製造現場に携わる多くの企業から注目を集めています。
2. スマートファクトリー実現のメリット
スマートファクトリーを実現すれば、製造現場の効率化に繋がるさまざまなメリットを得ることが可能です。
ここでは主な3つのメリットを紹介します。スマートファクトリー実現後のイメージをつかむためも、それぞれのメリットを理解しておきましょう。
データの見える化
スマートファクトリー実現により、製造現場データの見える化ができます。
例えば、設備の稼働状況や生産プロセスなどを見える化できるようになります。属人化により作業進捗が見えにくい工程も、監視担当者がリアルタイムで確認できるようになります。
作業進捗をリアルタイムに確認できるようになると、製造現場を客観的に把握可能な点がメリットです。
工場間の連携
スマートファクトリーを推進することで、工場間の連携がスムーズになります。
工場間の連携により、受注・生産情報のみならず検品結果等あらゆるデータを分析し、生産状況や生産工程の改善点・課題を共有することができます。
従来工場でトラブルが発生した際には、その工場内で対応しなければなりませんでした。しかし、工場間で連携を取れるようになると、別の工場で製造分をカバーするなど、柔軟に対応できるようになります。
製品の需要・供給予測が可能
スマートファクトリーを実現すれば、需要や供給の予測シュミレーションが容易になります。
例えば、市場のデータをもとに需要を予測するAIシステムを導入すると、需要が高まる時期に合わせた製品の提供ができます。
また、新たな生産ラインを導入する際に、供給量や稼働量を算出できるようになることもメリットです。適切な設備投資や在庫量の調節が可能となるため、経営資産の無駄を省くことにもつながります。
3. スマートファクトリー推進で気をつけるべきポイント
スマートファクトリー推進を成功させるために、気をつけるべきポイントを3つ紹介します。
データの扱い方を決めておく
スマートファクトリー実現に向けて、データの取り扱い方法を決めることは非常に重要です。
生産ラインに関するさまざまなデータを分析し、うまく活用する必要があります。しかし、システムで集められるデータ量は膨大となるため、むやみにデータを蓄積しても使えなければ意味がありません。
したがって、分析したいデータを決めた上で蓄積してくことで、データ管理の手間が減少し、グラフ作成などの分析もスムーズに行うことができます。
なお、データの扱い方に不安がある場合には、システムのメーカーやデータ分析の専門家に知恵を借りるのも一つの方法です。
システムのセキュリティ対策を行う
スマートファクトリーでは、データ管理をシステム上で行うためセキュリティ対策が重要です。
製造現場の大切なデータが流出しないように、マルウェア対策や不正アクセスの防止等、IT・AIシステムのセキュリティ対策を万全に行わなければなりません。
セキュリティサービスの導入もセキュリティ対策の方法として挙げられます。導入コンサルティングを受けセキュリティリスクを発見し、適切なセキュリティサービスを導入します。また、導入後もセキュリティサービスの監視や解析をサポートしてもらいます。
大規模システムには莫大なコストがかかる
スマートファクトリーを本格的に実現しようとすると、IoTセンサーやネットワークカメラ、AIシステム等の導入が必要となり導入コストや維持費がかかります。スマートファクトリーの実現に向けて本来の目的を明確にし、工場の規模感や必要な機器等の洗い出しなど整理を行ったうえで、適切な予算を組む必要があります。
いきなり大規模な設備を導入するのではなく、小規模な工程からスマートファクトリーに必要なシステムを少しずつ導入するとよいでしょう。初期段階では、自動で工程の割り当てが可能な生産スケジューラや、データの一元管理を実現するERPの導入が適しています。
4. スマートファクトリー実現まで
スマートファクトリー実現を目指すにあたり、重要な4つのステップについて解説します。
STEP1から順番に進めていければ、スマートファクトリー実現を成功に近づけることができます。
このステップはスマートファクトリーに限らず、例えば新しいITツールや業務システムを導入する際にも役立ちます。
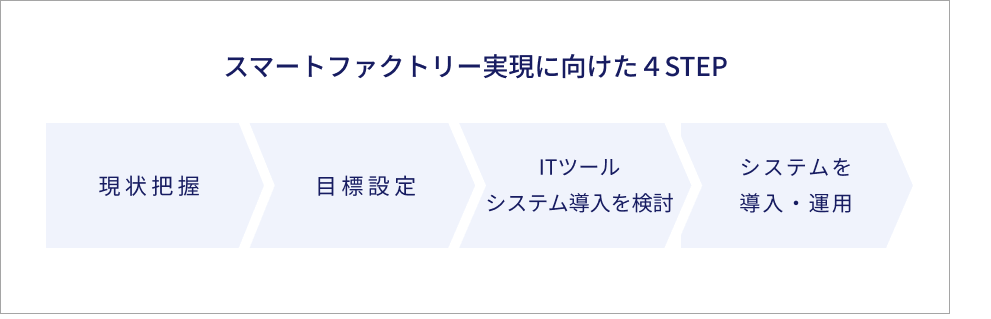
STEP1:現状を把握する
まずは、現状を漏れなく把握することです。
スマートファクトリー実現のためにITツールを導入しようとしている業務、システム利用、課題などを洗い出します。すべての業務を網羅することは大変な作業になりますが、どんなケースがあるか先に把握しておかないと、後から問題点が見つかり、システム導入途中に手戻りや遅延が発生する場合があります。
また、後から問題点を見つけることもできずそのままシステム導入してしまい、結局使えないシステムになりかねません。
現状把握は自社で行う方法もありますが、第三者に任せる方法もあります。第三者に委託すれば、自社の生産プロセスや業務内容を客観的に捉えられます。
STEP2:理想を決める
現状把握ができたら、次にスマートファクトリーの実現で得たい理想の姿(目標)を決めます。達成度合いが確認できるよう、具体的な数字を設定するとよいでしょう。
例えば、「歩留まり率〇%削減」「製造リードタイム〇分短縮」などです。STEP1で整理した現状の課題から設定するとよいでしょう。
生産リードタイムの短縮を目標に掲げた場合、達成のためにどの工程の無駄を省くべきか把握する必要があります。そこでまずは生産スケジューラを導入して現状を見える化するし、より効率的なスケジュールへ組み直しましょう。その後、工程の自動化や人員の再配置を実施し、段階的に生産リードタイム短縮を実現しましょう。
また、いつまでに達成するか期限もしっかり決めておくと、進捗の遅延を低減できます。
STEP3:ITツール・システムの導入を検討する
課題と理想の整理が終わったら、次はその理想を実現するために必要なITツール・システムの検討に移ります。
スマートファクトリー実現を支援するシステムや設備はたくさんあるため、より自社の運用と目的に合った設備やツールを選ばなければいけません。例えば生産計画システムとひとえにいっても、多数の企業がサービスを提供しています。どのサービスが自社に適しているのか「課題解決に向けた機能」「運用方法」の観点から見極める必要があります。また、アフターフォローや保守サービスの充実した企業を選ぶことも大切です。
具体的な検討を進めるにあたり、自社のデータを実際に取り込んで動作を確認できるお試し版の貸し出しや、体験セミナーの参加なども活用するとよいでしょう。
また、自社の業界に詳しいITベンダーであれば、課題の吸い上げも的確で意思疎通も早く理想の実現により近づきます。ITベンダーのHPには導入事例が掲載されていることがあるので、ぜひ参考にしましょう。
STEP4:システムを導入・運用する
検討したシステムのなかから自社に適切なものを導入し、運用します。
システムを有効活用するためにはいきなり大規模なシステムを導入するのではなく、スモールスタートから始めるとよいでしょう。まずは小規模システムを導入し、データの分析やモニタリング作業を行います。システムを運用していくなかで次に取り組むべき課題を明確にし、少しずつ規模を拡大します。
ITベンダーは多くのシステム導入・運用の現場を見てきているので、困ったときは相談してみるとよいでしょう。
5. スマートファクトリーの導入事例3選
ここでは、スマートファクトリーを実現した3社の事例を紹介します。各企業が得られた効果や解決できた課題に注目しつつ、自社の現状・課題と照らし合わせてみてください。
品質の向上に成功したA社の導入事例
自動車のエアバッグ用インフレータの製造を行うA社では、数人の熟練工が同時に定年退職することになり、熟練工のノウハウや技能の継承が課題となりました。
そこで、熟練工のノウハウや技術の見える化を目指すことになりました。具体的には、熟練工の作業動作を解析しデータとして登録できるシステムを開発したのです。
このシステムを導入した結果、新人技能工でも高品質な製品を製造できるようになり、安定した品質の製品を提供できるようになりました。
生産性の向上を実現したB社の導入事例
機械製造を行うB社では、工程毎の負荷を把握することができず、要員の適正配置が難しいことが課題でした。そのため、要因の残業や手持ちが発生していました。
そこで、工程毎の生産能力を定義し、工程負荷を考慮したスケジューリングを行う生産計画システムを導入しました。
導入の結果、負荷状況の見える化によって、各工程にあたる要員数を変更した場合のシミュレーションが可能となり、要員の適正配置に貢献しています。
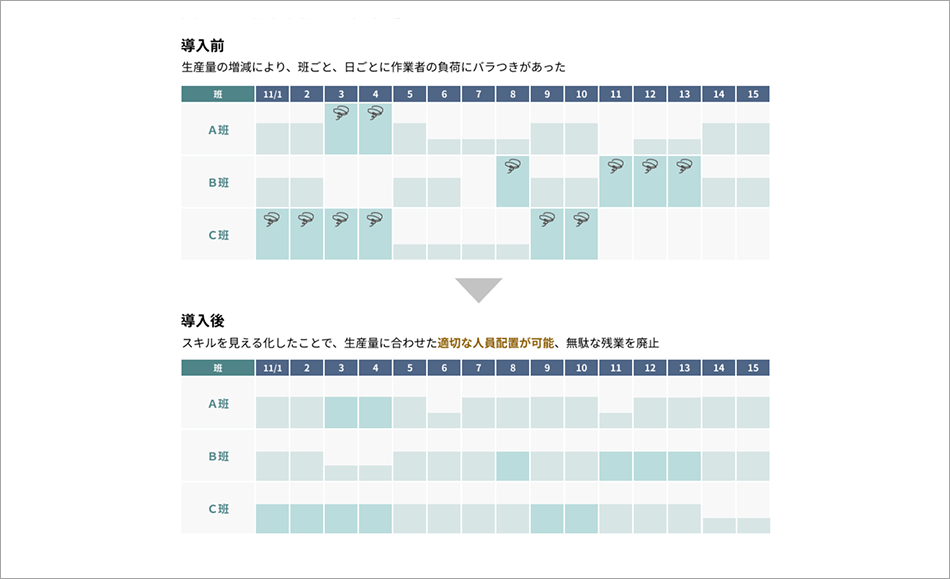
稼働異常への迅速な対応が可能になったC社の導入事例
プラスチック製品の生産を行うC社では、工場の稼働状況を作業員が見回りで確認し、成形機における1ショット当たりの成形時間等に異常があった際、対応しなければならない点が課題でした。
そこで、成形機にカメラを設置し、稼働状況をタブレットで確認できるシステムを導入しました。異常を検知すると、タブレットを通じて管理者へ通知されます。
システム導入の結果、24時間体制での自動生産が可能になり、異常への迅速な対応も可能になったのです。
6. スマートファクトリー実現にはまず生産スケジューラを導入しよう!
スマートファクトリーの実現を進めるためにお勧めしたいツールの1つが生産スケジューラです。
生産スケジューラとは、設備や作業員が行う工程を割り当てるツールです。どの機械・装置でどの受注に対してどの作業をすれば効率がいいのかを割り出し、無駄のない計画を立てられます。
ここからは、生産スケジューラがなぜスマートファクトリー実現の第一歩に適しているのかを解説します。
生産スケジューラが推奨される理由
生産スケジューラは、スマートファクトリー実現へのスモールスタートに適しています。
生産スケジューラは生産状況を見える化し、余剰在庫や滞留時間など生産工程の問題を明らかにします。これにより、問題解決に最適なAIシステムやIoTの導入が可能となり、スマートファクトリー実現を加速させます。生産スケジューラは、生産工程の完全自動化に成功したスマートファクトリー実現への重要な一歩となるのです。
なかでも、生産スケジューラ「FLEXSCHE」は、柔軟性が高くカスタマイズできる点が特徴です。生産品目が多くても計画の立案が可能であり、生産工程の見える化を実現できます。
生産スケジューラ「FLEXSCHE」についてのご相談は、お気軽にお問い合わせください。
スマートファクトリーを実現する
生産スケジューラ「FLEXSCHE」