Case
導入事例
FLEXSCHEを使うことで、生産計画の見える化を実現。
これまでの課題だった要員配置や余剰在庫の問題も大きく解消されました。

機器製造業
同社が抱えていた課題とFLEXSCHE導入の背景
- Excelで生産計画を管理していたため、工場内の負荷状況を充分に把握できず、製造納期も不明確であった
- 工場の生産能力に基づいた計画を立てられないため、販売予定と生産可能量のバランスが取れず、受注機会の損失が発生していた
- 生産計画を工程単位で行ってこなかったことから、工程毎の負荷を把握することができず、要員の適正配置が難しい。工程毎にかかる負荷バランスにバラつきが生じ、結果的に要員の残業や手待ちを発生していた
- 複数拠点間の生産計画が連動していないため、調整に時間を要していた
- 上記の課題を解決すべく、各種システムを比較検討した結果、宇部情報システムが導入を支援する生産スケジューラ「FLEXSCHE」が自社のニーズ・要件に合致し、導入する運びとなった
FLEXSCHE導入により実現できたこと
- FLEXSCHEに工程毎の生産能力を定義することで、工場内負荷状況の見える化を実現した
- 販売予定情報から生産計画を立案する際、工程負荷を考慮したスケジューリングを行い、適正な生産可能量の把握・納期判断が可能となった
- 負荷状況の見える化によって、各工程にあたる要員数を変更した場合のシミュレーションが可能となり、要員の適正配置に貢献した
- 複数拠点における生産計画の運用をFLEXSCHEに統一し、全工場の生産能力および工程毎の負荷状況を見える化することで、生産管理部での一元管理が可能となり、生産計画業務の効率化を実現
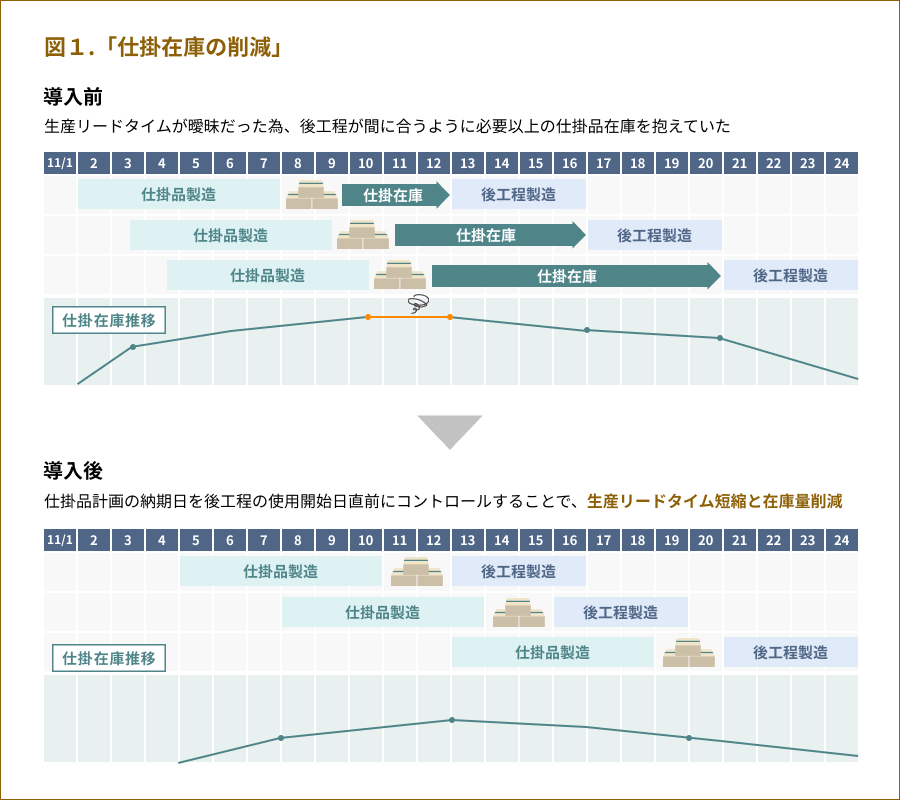
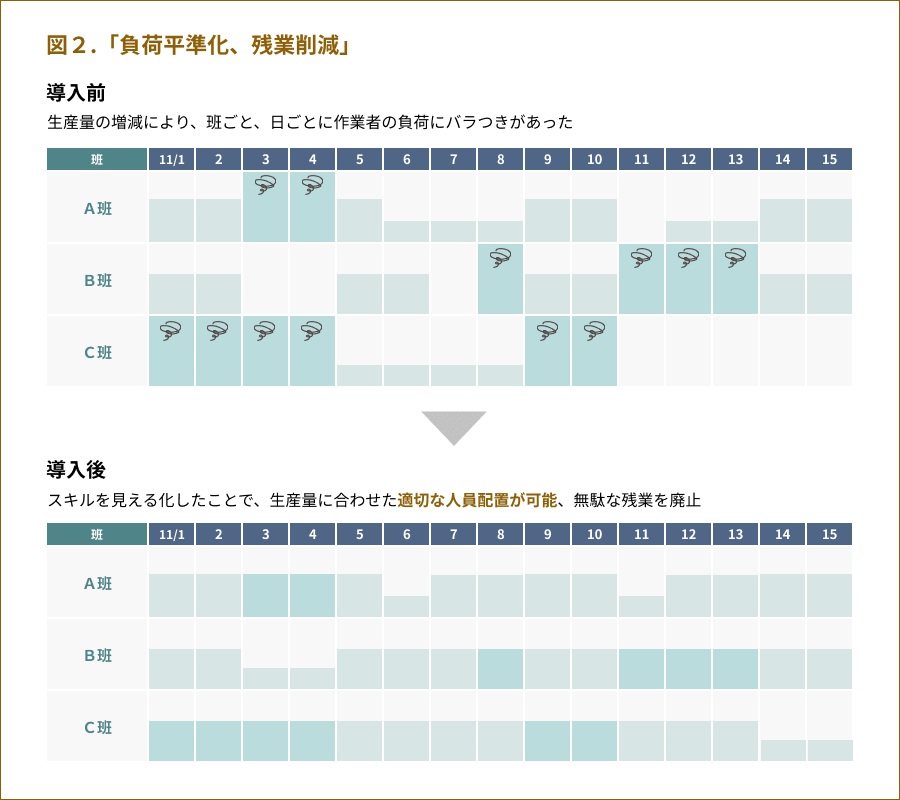
お客様の声
-
仕掛品在庫25%削減
「工程毎の生産リードタイム把握が曖昧だったこれまでは、後工程を考慮すると生産ラインを止めることもできず、必要以上の仕掛品在庫を抱えるような状況でした。FLEXSCHEを導入したことにより、後工程の使用タイミングに合わせ仕掛品を供給することが可能となったことで、余剰在庫の削減につながりました。今後もFLEXSCHEを活用して、更に在庫削減ができるよう挑戦していきたいと思います。」 -
生産人員の適正化、直接作業人員4.8%省人化
「従業員個々の生産能率やスキルを見える化したことで、適切な人員配置が可能となりました。ある工程では、効率化の成果もあり、従業員の勤務体制を3交替から2交替に変更することもできました。また、生産数増減時はFLEXSCHEによるシミュレーションを行うことで、常に適正な人員配置が維持できています。」 -
生産計画立案業務の一元化/最適化
「生産計画の立案業務は、様々な部署の人間が携わってきましたが、FLEXSCHEを導入したことで、生産管理部による情報の一元管理が可能となり、関わる人員数の最適化が図れました。その結果、削減した時間を他の業務に充てるなど、生産管理の最適化だけでなく、従業員個々が浮いた時間で現場の改善にも力を注げるようになるなど、時間の有効活用にもつながりました。今回のFLEXSCHE導入で培ったノウハウを海外工場にも展開できればという構想を立てているところです。」
スマートファクトリーを実現する
生産スケジューラ「FLEXSCHE」