導入事例
我々の要求を全て満たしてくれるパッケージを探したら「FLEXSCHE」しかありませんでした。
「無理」と言わない宇部情報システムのおかげで、世界初の、環境分析業向けに最適化された計画システムが完成しました。
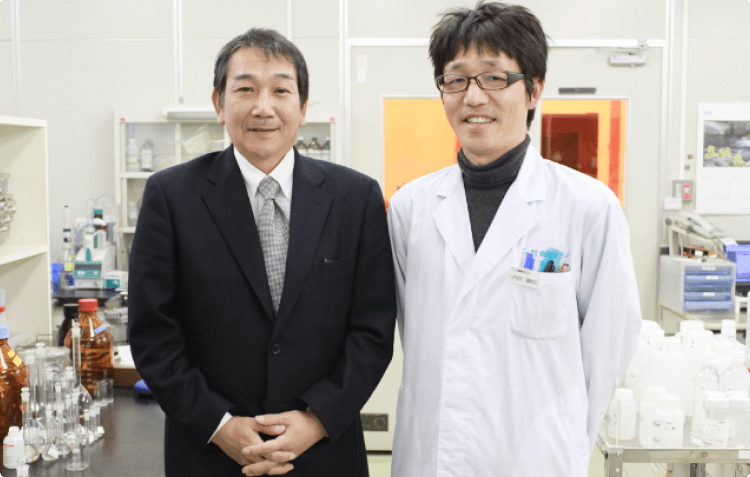
株式会社東海テクノ
代表取締役 市田 淳一氏(左)
環境事業部 四日市分析センター ラボGr 課長 戸田
勝也氏(右)
東海地方を中心に環境調査分析事業を展開する株式会社東海テクノは、「少量超多品種」の分析業務を効率的に行うため、環境分析業として世界初となる作業計画システム構築に着手しました。生産スケジューリング・パッケージ「FLEXSCHE(フレクシェ)」をベースにどのようなシステムが構築されたのか、また開発を担当した宇部情報システムへのご評価を、代表取締役 市田淳一氏と、環境事業部 四日市分析センターラボグループ課長 戸田勝也氏にうかがいました。
「FLEXSCHE」をベースとした作業計画システムの構築を依頼
― 宇部情報システムへのご依頼内容を教えて下さい。
当社(東海テクノ)は、宇部情報システムに、生産スケジューリング・パッケージ「FLEXSCHE」をベースとした、分析業務の作業計画システムの構築を依頼しました。製造業向けのパッケージを分析業向けにカスタマイズしたため、難しい要求もあったと思いますが、根気強く対応していただき、要求通りのシステムが実現しました。2011年11月ごろから要件定義、翌2012年2月から開発フェーズが始まり、本格的に稼動し始めたのは、2014年1月です。
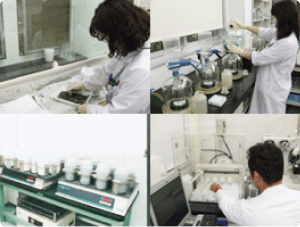
短納期を実現する大量検体処理体制が東海テクノ社の強みの1つ
― 環境分析を行う御社がなぜ、製造業向けのパッケージを選んだのでしょうか。
スケジューラという製品は製造業向け以外には存在しないからです。そのスケジューラの中で、我々の要求に合わせて柔軟にカスタマイズできるパッケージを探して、「FLEXSCHE」を選びました。他に比較するほど製品はありませんでした。
もともと創業者が産業機械のエンジニア出身だったということもあり、当社の分析業務の作業プロセスは、製造業的な視点で構築してきました。当社の創業のきっかけは、高度成長期、大気汚染防止法に基づくばい煙測定業務を開始したことですが、国内の産業が成熟し物作りが海外に移転し始めると、工場の閉鎖や遊休地の売却に伴う土壌分析が増えました。これらの分析は検体が大量に発生します。そこでオリジナルの自動化装置を開発するなどして、大量検体が発生する案件に対応してきました。それが当社の強みの1つとなっていますが、それはあくまでも部分最適化です。自動化した工程は一気に作業を進められますが、自動化できない工程は一気には進められません。より効率化を進めるためには、人員の配置や装置の手配を含めた全工程を最適に計画できるマネジメントシステムが必要でした。それが、宇部情報システムへの依頼につながったのですが、その課題解決には10年以上の月日がかかっています。
「FLEXSCHE」以前に導入していた生産スケジューラで直面していた問題
―「FLEXSCHE」導入までの10年強の間は、何らかのシステムを導入されていたのですか。
当社は宇部情報システムに「FLEXSCHE」をベースとした計画システムの構築を依頼するまでは、別の生産スケジューラをカスタマイズせずに導入して、苦労しながらもなんとか使いこなそうと試行錯誤していました。
日本の製造業の生産管理は世界一です。日本の製造業が使っているシステムを使えば、私たちの課題も解決できるだろうと考えました。もちろん製造業向けのシステムが分析業でそのまま使えないことも承知していましたが、当時は、どう最適化すれば良いのかという正解を持っていなかったので、逆にシステムに合わせてみようと考えたのです。ところが、あまりにも違いすぎて、3~4ヵ月ぐらい使ってみて、合わせることは不可能だという結論に至りました。
― カスタマイズ、または、細かい設定などができないパッケージだったのでしょうか。
これまで使っていたシステムは、カスタマイズして使うことを前提としたパッケージではありませんでした。また、構造もブラックボックス化されていて、どのような仕組みで割り付けが行われているのかが見えませんでした。色々なパラメーターを触れるようにはなっていますが、やってみないとどうなるかがわかりません。結果が出る度に、数字を減らしたり増やしたりして計算し直すということを繰り返しても、そのまま現場に作業指示として渡せる結果は得られませんでした。
装置によっては、分析する物質によって、装置の設定を変えなければいけないものがあります。その設定に半日を要するものもあります。したがって、1日の作業の中に効率よく装置分析の作業を割り付けるためには、作業内容が切り替わる際に、システムが前の作業で分析していた物質を理解して、次の工程で設定を組み直す必要があるのかどうかを判断しなければいけません。しかし以前使っていたシステムは、そのような細かい設定はできません。半日分の時間が計画に反映されなければ、計画を立てる意味はありません。
― 以前のスケジューラは、そのまま使わなくなってしまったのでしょうか。
毎日同じことを繰り返す工程だけで使っていました。例えばサンプリングしてきた土を袋から出すなどの簡単な工程です。大量検体を扱う場合は派遣アルバイトを手配します。その際に、何人日必要かを判断する目安ぐらいには使えました。
また、システムの導入には大きな投資をしたので、簡単にあきらめるわけにはいきません。得られた結果をアレンジして、何等かの役に立てられないかとさらに投資をしながら何年も試行錯誤を続けましたが、思惑通りに使えるようにはなりませんでした。
分析業において精度の高い作業計画が必要な理由
― 製造業と分析業の違いは、どのようなところでしょうか。
製造業にたとえた場合の生産ラインがマルチで動くところです。
製造業では、1つの工程を複数の人が入れ替わり立ち代わり作業することはありません。当社では、1人の分析スタッフが、平均5つの工程を担当し、かつ、装置を複数のスタッフで共有しています。したがって、分析スタッフと分析装置をいかに効率よく割り付けることができるかが重要となります。
当社の分析センターで行う分析業務は、検体の種類や分析項目によって約1,500種類もの分析プロセスに分かれています。言うならば1,500種類の製品を作る生産ラインがあることになります。ただしどの分析プロセスも扱う量は少量であり、毎日、常に決まったラインを動かしているわけではありません。約1,500種類のうち、毎日、バラバラの組み合わせで20種類ぐらいの分析を行っています。
各分析プロセスは、少なければ3つ、多ければ10以上、平均すると5つの工程に分かれていますが、当社の分析センターでは、業務効率を上げるために、1つの分析プロセスを1人の分析スタッフが最初から最後まで担当するのではなく、各分析プロセスに共通する工程を可能なかぎりまとめて、それぞれの分析スタッフに割り振っています。1人平均5つの工程を担当していますが、このように1人のスタッフが5つもの工程を担当するという部分が製造業との最大の違いです。
さらに問題を複雑にしているのは納期です。
当社の管理する納期は大まかに分けると3種類あります。厳密な期限が指定される「絶対納期」、緩やかな範囲を持った「希望納期」、日程はこだわらない「おまかせ納期」の3つです。
「絶対納期」の案件の中でも、特に厳しいのが製品の品質に関わる分析です。製品といっても最終製品ではなく部品や素材です。これらは本当に少量で、1検体のみという場合も少なくありません。しかも突発的に発生して、納期も短い。このような突発的な案件が入ってきた際、それを1日の業務の中で、誰にどのように割り振っていけば良いのかという判断は非常に難しい問題です。人の配置だけではなく、装置の割り付けも同様です。ほとんどの装置は、沢山の分析で共用していますので、計画の精度が落ちると、使いたい時に使えないということが発生します。スタッフ同士がコミュニケーションをとっても、明日どうなるかわからないのでできるだけ独占したいという心理が働きます。お互い迂闊に「明日何時には空く」と言ってしまえば自分の作業が滞るかもしれないので、調整が難しくなってしまいます。
このように日々の作業計画を立てる術がないため、明日はどうなるかわからない。そのため「今日やれるところまでやろう」と考えて、夜遅くまで残業することになってしまう。マネージャークラスも「とにかく頑張れ」としか言えない。このような状況から脱却して「今日は、これだけやってくれれば大丈夫」という指示ができる環境作りは、当社だけではなく、業界全体の課題でもあります。
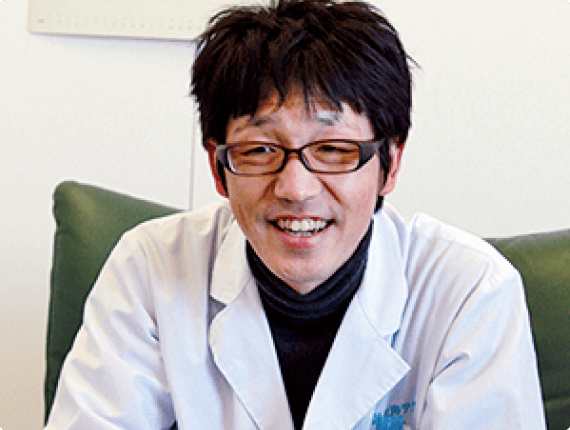
初めて携わる分析業のことを大変よく勉強していただき、
要求通りのシステムが実現しました。(戸田氏)
― それがスケジューラを導入するきっかけだったのですか。
スケジューラを導入した直接のきっかけは、根拠のある納期回答がしたかったからです。
当時は、ちょうど工場用地の移転・売却などに伴う土壌分析の案件が増加した時期です。受注するためには指定された最終納期に間に合わせることができるということを、正式に回答しなければいけません。指定納期への可否回答のスピードが受注を決めるような状況でした。
しかし、分析作業を行う現場は、「無理だと"思う"」といったあいまいな回答しかできない状況でした。それに対して、何としてでも受注したい営業からは「社長の力で、徹夜してでもやらせて欲しい」という要望が上がってきていました。そのような案件が1件や2件ではなく、沢山ありました。会社としても受注したいのはやまやまですが、現場に根性で乗り切れとは言えません。1件、2件、根性で乗り切ったとしても、いつまでも続けられるものではありません。ましてや無理な受注による納期遅れはその後の取引に致命的な影響を与えます。現場が対応できるようにするためには、迅速にきちんとシミュレーションをして、精度の高い計画を立てる必要がありました。逆に営業に不可能と回答する場合には、できない根拠を示す必要がありました。お互いのわだかまりを解決するには、システム化するしかない。そう考えて、以前のスケジューラを導入しました。
こういった経緯もあり、スケジューラは当社の競争力につながるはずのものでもあったのですが、導入のきっかけとなった課題は一向に解決しませんでした。そこで、以前のスケジューラを活かすことは諦めて、考え方を180度変えて再スタートしようと着手したのが今回の「FLEXSCHE」導入です。
自社が要求するシステムを構築できるパッケージは「FLEXSCHE」しかなかった
― 再スタートにあたってはどのように考えましたか。
「世界に誇る製造業が使うシステムをそのまま使う」という考え方はやめました。以前のスケジューラを使用する中で、我々にとって何が必要なのかが大体わかりました。そこで我々が要求する仕様を作り上げることが可能なパッケージを探して、それをベースに構築していこうと考えました。
その結果、該当するパッケージは「FLEXSCHE」しかありませんでした。それでもかなりカスタマイズする覚悟で選びました。実際にでき上がったシステムは、「FLEXSCHE」と本当に言える部分はインターフェイスやデータをエクスポートするなどの操作性に関わる部分ぐらいです。システムの主要部分はほとんど宇部情報システムにカスタマイズしてもらって制御しているのが実態です。
― 宇部情報システムに依頼した理由を教えて下さい。
依頼先の選定方法はインターネット検索です。「FLEXSCHE」で検索してヒットしたのが宇部情報システムでした。宇部興産の関連会社なので間違いないだろうと迷わず決めました。
パッケージも委託先も迷いませんでしたが、最終的な発注まではじっくりと時間をかけました。これまで我々が苦労してきたことをベースに、「FLEXSCHE」ならどのように解決できるのか、デモを作ってもらって実際に動くイメージを確かめました。もちろん、デモを組むにあたっては、ある程度の予算を割く必要はありましたが、感覚で始めると失敗することは身にしみていたので、我々がこれまでに困っていたことや要求したいことは全て伝えてデモを作ってもらいました。それによって検体数が少なければ要求通りの動きをすることが確認できたので、正式に発注しました。
最重要ポイントは「工程のまとめ」
― 今回開発したシステムのポイントを教えて下さい。
今回、作業計画システムの開発にあたっては、当社から宇部情報システムにさまざまな要望を出しており、それらの要望は、ほぼ完璧に反映していただきました。特に重要なポイントは以下の6つです。
(1)仮受注の入力と迅速な納期回答
(2)工程のまとめとロット化
(3)人員および装置状況の把握とシミュレーション
(4)タブレットとバーコードリーダーの活用による作業指示と実績入力
(5)歩留りの把握
(6)残業管理・負荷管理
(1)仮受注の入力と迅速な納期回答
まずは長年の課題であった迅速な納期回答の実現があります。今回、構築した作業計画システムでは、仮受注を入力できるようになっており、それによってシミュレーションして納期を確認することができます。これで長年の課題が解決しました。
(2)工程のまとめとロット化
その上で、今回構築したシステムの最も重要なポイントは、工程のまとめとロット化です。
分析業務は種々の工程を経て実行されますが、先ほども申しあげたとおり、案件によってその分析工程は異なります。しかもそれが毎日異なる組み合わせで20種類ぐらい動いています。これを効率化するには、各案件の工程をバラバラにして、一度に実行できる工程をまとめ直す必要があります。また工程をまとめることで、1つ1つの作業に専念でき、誤作業を未然に防ぐことができます。
工程をまとめる際に考えなければいけないのが納期です。今日やらなくて良い案件までまとめてしまうと際限なくなってしまいます。そのため同一時期に実施すべき作業をまとめ、1日の最大可能数を上限として割り付け、作業指示に反映させます。これをロット化と呼んでいます。
このように工程でまとめた上で、時間軸でロット化するという、2段階のまとめを行うことでより効率的な計画を組むことができるようになりました。
(3)人員および装置状況の把握とシミュレーション
当社の分析業務は、有機物グループと、無機物グループに分かれて行っています。しかし案件の入り具合によって、それぞれのグループで必要な人数が変わります。状況に応じて配置を変える判断ができるようにすることで人のマネジメントができるようにしました。
装置の手配についても同様です。システム導入の契機となった指定納期可否・受注可否回答についても、営業サイドだけで判断できない(休日出勤、残業、人繰りをすれば可能)ケースでも、例えば、「この作業に1人増やしたら」、「休憩をずらせば」、「休日出勤すれば」、「何時間残業すれば」等の仮説を簡単にシミュレーションして判断できるようになりました。
(4)タブレットとバーコードリーダーの活用による作業指示と実績入力
今回開発した作業計画システムでは、作業指示の表示と実績入力にタブレット端末とバーコードリーダーを採用しました。特に実績入力は、作業項目ごとに入力しなければいけませんので、いちいちパソコンに戻って作業しなければいけないのはストレスにもつながります。
また、タブレット端末の活用によって、今後、できることがさらに増えます。タブレット端末の導入で、現場の作業効率をドラスティックに向上させたいという意図もありました。歩留りの把握もその1つです。
(5)歩留りの把握
分析業界には特有の歩留り問題があります。分析業界の歩留り問題というのは、再分析が発生していても、それを正確に把握できないということです。社員の行動を見ているだけでは、それが初めての作業なのか、やり直しの作業なのかは判断できません。再分析によって実際には実績の1.5倍ぐらいの仕事量となっていると考えられます。この部分を削減することができれば、さらに効率化することができます。また、やり直しが発生する要因は、単純なミスもありますが、特定の項目や検体で頻繁に発生することがあるため、それらの特性によって引き起こされやすいという場合もあります。したがって再分析が発生する要因を検証して、改善できれば、それは当社のノウハウになります。
再分析が発生する要因を検証するには、再分析が発生したという事実と、それがなぜ発生するのかを正確に記録する必要があります。これまでそれは不可能だと考えていました。その理由は、そのためのシステムがなかったからです。専用用紙で申請するようなルールを作ったとしても、それができる状況ではありませんでした。
しかし、今回、作業計画システムを構築するにあたっては、その再分析も作業計画に反映されなければできないシステムにしました。実績入力をする際に、再分析が発生する旨を入力します。すると翌日の作業計画と作業指示にそれが反映されます。入力する際には再分析の理由も必須項目としていますので、そのデータが蓄積していけば、ノウハウになっていきます。
こうやって集めたデータは使わないことが一番罪です。集めたデータを活用することは、会社にとっても作業をする社員にとってもメリットにつながります。
(6)残業管理・負荷管理
精度の高い作業計画が立てられるようになり、再分析の管理ができるようになったことで、残業管理が可能となりました。就業規則上は、上司の許可を得なければ残業できないとなっていますが、これまでそんなことをやっている社員はいませんでした。しかし新しいシステム上では、作業指示に反映された仕事しかできません。再分析が発生したことが理由で翌日の作業量が増えた場合でも、理由が明確ではない残業はなくなります。結果として理想の残業管理ができるようになりました。
また、人、設備、機材などの負荷が視える化されるので、不足資源やボトルネック工程の把握、技術教育の優先度を認識できるようになりました。
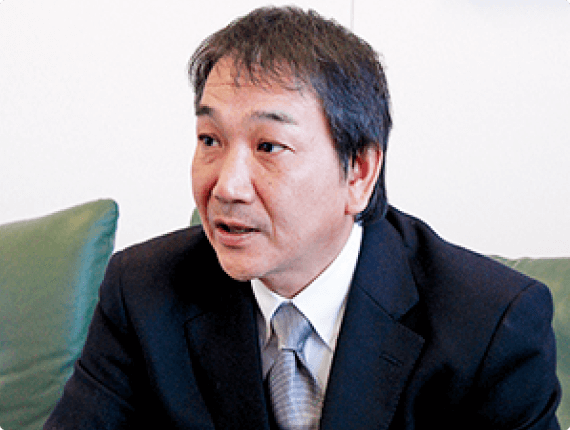
長年の課題だった迅速な納期回答ができただけでも大変満足しています。
(市田氏)
― 本格稼動して2ヵ月がたちましたが、思惑通りに活用できていますか。
毎年、2月、3月は仕事が多い時期です。特に今年は不動産が動きはじめて、非常に多忙な時期と重なったため、まだ成果を測れるほど使いこなせていません。
ただ、言えることは、担当者ごとのばらつきがなくなりました。今まではざっくりした作業計画のもと、実際の工程は現場で思い思いに組んでいたため、スキルによって作業の進捗が遅れるということがありました。しかし、今は計画に基づいた作業指示があることで、個人差がなくなり、いつも特定のスタッフだけが残業している、ということはなくなりました。
宇部情報システムに対する評価
― 今回、開発はスムーズに進みましたか。
発注前のデモンストレーションが良かったので、簡単に構築できそうだと思っていましたが、実際の開発は難航しました。現実の業務の中では検体数も増えて工程が複雑になり、デモンストレーション通りにはいきませんでした。要求どおりに開発しても、アウトプットされた結果が予想外ということもありました。また、1,500通りの工程分のマスターを用意するのにも時間がかかりました。しかし、今回は多少納期が遅れてもとにかく完璧なシステムを作りたい気持ちの方が強かったことと、予想外の問題が発生したとしても力技で何とか解決できそうな感覚は常にあったので、私たちも妥協することはありませんでした。
そんな中で、2013年2月に有機グループでの運用を開始しました。この段階ではまだ完全なシステムではないことを承知した上でスタートしています。現場でタブレット端末を運用することが初めてなので、タブレットに慣れることと、作業指示や実績入力画面の視認性や操作性の問題点を洗い出す目的がありました。一方で、計画システムそのものの修正を重ねて、2014年1月に何とか安定して動かせるようになりました。
― そのような開発を経た上で、宇部情報システムにはどのようなご評価をされていますか。
宇部情報システムには、この難しい問題によく付き合っていただきました。当社は宇部情報システムにできないと言われたらどうしようもありません。無理難題に近い要求も結構あったかもしれませんが、無理だと言わずに、何とかしてくれようとしてくれたことが嬉しかったです。タブレット端末も、OSがすぐに変わるし、機種のモデルチェンジも早いので、なかなか安定的に動かすことは困難ですが、頑張って組み込んでいただくことができました。
また、分析業のこともよく勉強していただいて、プラスアルファの提案をしていただけたことも良かったと思っています。例えば、工程のまとめとロット化にあたっては「同一時期」の考え方を提案していただいて、当社の業務にフィットするまとめ方が実現しました。また、工程のまとめ方も、比較的単純な作業工程の前処理と、複雑な動きをする装置分析とで、まとめ方を変えるといった提案もあって、より精度の高い計画が組めるようになりました。
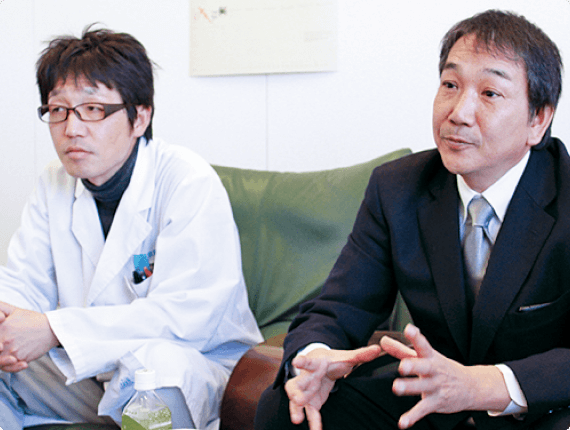
計画や実績入力で蓄積したデータは、歩留りの解析など、さまざまな活用方法が考えられます。
(右:市田氏、左:戸田氏)
今後のビジョンと宇部情報システムへの期待
― 今後のビジョンをお話し下さい。
本格稼動後の期間が短いため、まだ成果を検証できていませんが、多忙な時期が終わればより詳細な検証ができるようになります。納期遅れが発生しなければうまく機能しているということだと考えています。残業時間についても、全体の仕事量に対して適性だったかどうか、4月以降、検証していきたいと考えています。
また、今後は、このシステムに入力した計画と実績のデータを活用して、その差を見ることでの運搬リードタイムの改善課題の抽出や原価管理、歩留りの解析などへと発展させていきたいと考えています。
― 最後に、宇部情報システムへのご期待をお話し下さい。
現在、当社は宇部情報システムとはサポート契約をしており、運用中、困ったことがあれば、連絡してサポートしていただいています。今後は、リモートによるサポートを受けられるように電子会議のインフラを互いに整備していくことを検討しています。
我々分析業界はJISなどで決まった分析を"精度良く、早く、安くやる"という段階を超えて、そうした分析に追われることなく、更に資源・エネルギーや食・健康分野に人材や装置を振り向けていく段階に入っていると考えています。そこで切磋琢磨することが当社を含め業界の発展につながると信じているのです。
そこで、当社は、今回、構築した計画システムを、我々の同業に公開していこうと考えています。少なくとも現在、分析の業界でこのような生産計画ができている会社は、海外に目を向けても存在しません。当社が世界で初めて開発したわけです。しかし、自分たちの想いで作っただけなので、これを世界で通用する高次元なシステムに育てたいと考えています。そのためには、世界中の同業社に使っていただく必要があります。そして、他社に使っていただくためには、導入しやすい価格設定を含め、システムを拡散していくための戦略が必要となります。宇部情報システムには、そのためのご協力をいただきたいと考えています。
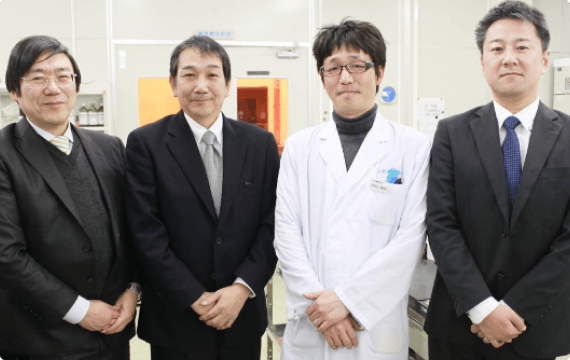
株式会社東海テクノについて

主に製造業において環境に負荷がかからない物作りを行うための環境調査・分析・コンサルティングなどを行う。典型7公害のうち地盤沈下を除く、土壌、排水、煙、音、匂い、振動といった全てを調査・分析の対象とする。三重県四日市市、松阪市に分析センターを持ち、製造業的な視点で構築した独自の分析プロセスや自動化装置を強みに、大量検体を短期間で分析するニーズにも対応。工場移転や遊休地売却に伴う土壌・アスベストなどの調査・分析では、全国からの依頼に応えている。
- 設立
- 1972年12月
- 従業員数
- 102名(2012年11月現在)
- 本社
- 三重県四日市市
スマートファクトリーを実現する
生産スケジューラ「FLEXSCHE」