Column
コラム
外観検査の手順やメリットを解説!自動化の先にある品質管理とは?
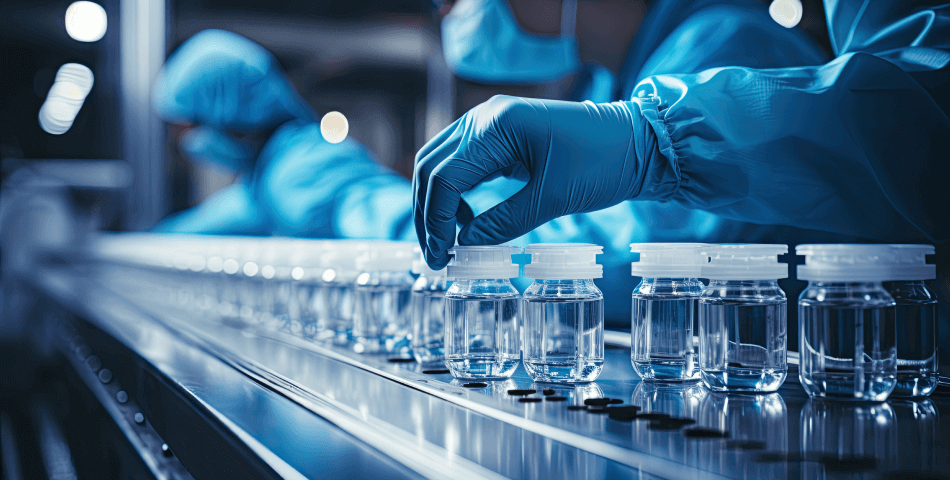
製造業において、品質を保つために重要な検査の一つが外観検査です。外観検査は目視検査や画像処理、AIを活用した方法があります。また、外観検査を自動化することで、人手不足対策や品質向上も可能です。
そこで、本記事では外観検査の手法や自動化におけるメリットなどを詳しく解説します。さらに、外観検査の自動化における品質管理業務で必要な点についても取り上げました。効率的な品質管理を目指している方は、ぜひご覧ください。
目次
1. 外観検査とは?
外観検査は、製造業において品質管理の一環として重要な役割を果たす検査業務です。外観検査では、製品で使用する部品の外観形状などが、仕様や規格を満たしているか否かを確認します。製造途中の製品を検査するのか、完成品を検査するのかなど、外観検査にはタイミングや手法による違いがあります。そのため、仕様や規格を満たすための目的に応じた検査を行なわなければなりません。
外観検査は、製品の品質向上のために必要な検査です。顧客満足度の向上や安全性の確保にもつながるため、ものづくりにおいて必要不可欠なプロセスなのです。
製造途中・完成時の外観品質を確認
外観検査を実施するタイミングを大きく分類すると、下記3つの工程となります。
- 外部から納入された部品や半完成品の受け入れ検査
- 製造途中の半完成品を検査する方法(工程内検査)
- 完成した製品を検査する方法(最終検査)
不良はなるべく早期発見し、下流へ流さないようにしなければなりません。これは製造途中の状態で不良が発生した場合に、途中の工程からやり直したり、不良品に対して後工程の加工を実行しないようにするためです。
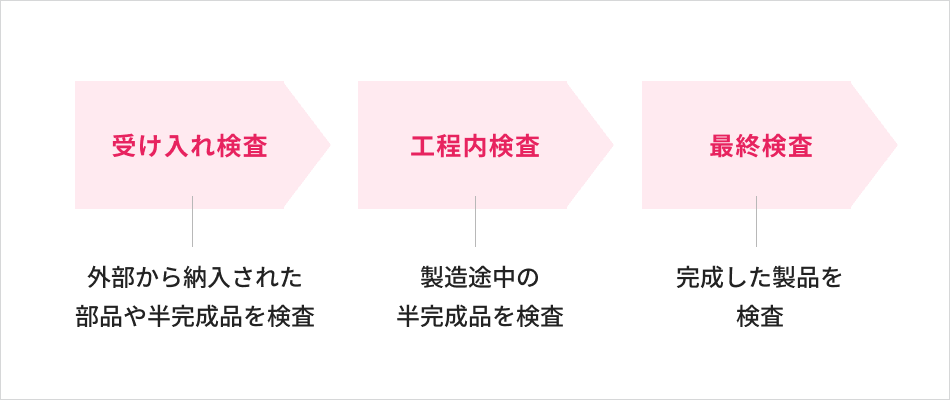
外観検査と目視検査の違い
外観検査というと機械によるチェックのイメージが強いかもしれませんが、現場では目視検査と呼ばれる方法も残っています。近年の製造業は自動化やDX化、AIによる自動化が進んできました。しかし、自動化が進んだ現在でも、目視検査が必要な場面もあります。
目視検査が重要視される理由は、より微妙な見た目の違いを判別できるからです。画像認識やAIが進化した今も、人間の判断能力の方が優れている場面が多々あります。
ただし、目視検査では顕微鏡レベルの違いを判別できません。また、ヒューマンエラーやばらつきが生じる可能性もあります。したがって、機械による外観検査と目視検査は目的に応じて使い分けるべきです。
2. 目的に応じた外観検査4種
外観検査は機械による検査、目視検査にかかわらずさまざまな方法があります。主な外観検査の方法は、下記の4種類です。
- インライン検査
- オフライン検査
- 抜き取り検査
- 全数検査
それぞれの検査方法は、検査の目的や製造物の種類・性質によって使い分けられています。この章では、実際に製造工場で実施されている上記4種類の検査方法について詳しく解説します。
インライン検査
インライン検査とは、生産ラインのなかに外観検査を組み込んだものです。インライン検査の特徴は下記の2点です。
- 全数検査に向いている
- 目視検査には不向きである
インライン検査は、生産ラインに組み込んで自動的に検査するため、全数検査が基本となる検査方法です。そのため、生産ラインに流れてくる大量の製品を素早く検査しなければならず、目視検査では不良品を見逃す可能性が高くなります。
ただし、制御方法によっては、生産工程の製品サンプルを一定数取り出してインラインで検査する方法もあります。
オフライン検査
オフライン検査はインラインとは対照的に、生産ラインに組み込まずに外観検査を行なう方法です。
オフライン検査の主な特徴は下記の3点です。
- 全数検査には不向き
- 精密な検査に最適
- 検査工数の多い検査に最適
生産ラインとは別のステーションでの検査となるため、生産ラインと同じ速度で検査する必要はありません。ただし、時間をかけて外観検査を行なう場合、生産速度に追従できないために全数検査に向いていないというデメリットもあります。
一方、検査に時間をかけられるため、精密な検査や工数の多い検査ができる点がメリットです。目視検査も同様の理由から高速の生産ラインではオフライン検査が実施されます。
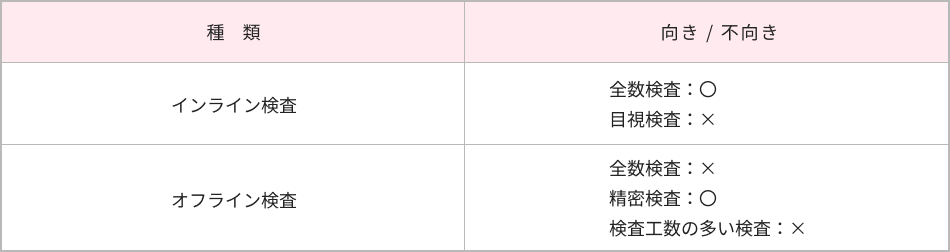
抜き取り検査
抜き取り検査とは生産された製品の中から、一定数のサンプルを抜き取って検査する方法です。
抜き取り検査の特徴は主に下記の3点です。
- 不良品が混入する可能性がある
- 生産量が多く安価な製品に最適
- 破壊検査に向いている
抜き取り検査を実施する製品は一部のサンプルであるため、サンプルに不良がなければ生産ラインを止める必要はありません。ただし、サンプルに連続して不良が発生した場合、何らかのトラブルが発生したと見なしてラインを確認することはあります。また、製品によっては傷をつける破壊検査が必要な場合もあります。全数を破壊することは不可能なため、抜き取り検査が最適です。
全数検査
全数検査とはすべての製品を検査する方法です。主に製品が高額な場合や品質が重大な事故にかかわる場合など、品質を高いレベルで保証しなくてはならない製品に実施されます。
全数検査ではすべての製品を検査するため、生産速度と同じ速度で外観検査を実施しなければなりません。極端に工数が少ない場合以外は時間と労力がかかるので、その点は全数検査のデメリットと考えられます。
また、製品価値がなくなる破壊検査も、全数検査には向いていません。
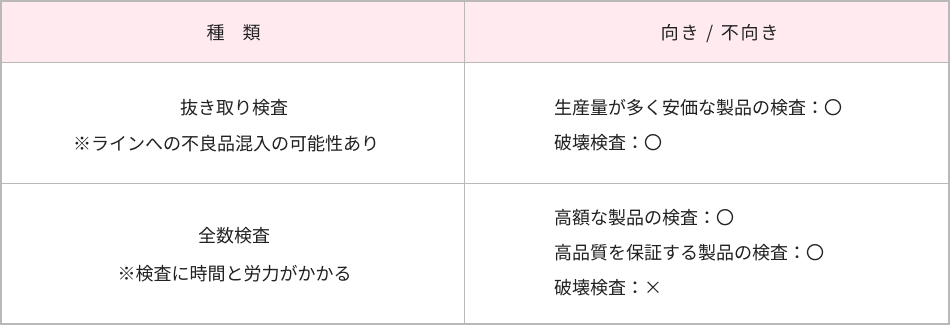
3. 外観検査の自動化で得られる3つのメリット
前述したとおり、外観検査には目視検査と機械による検査方法があります。目視検査も機械による検査も適材適所で利用することが重要です。
そこで、ここでは外観検査の自動化で得られるメリットについて紹介します。外観検査の自動化によるメリットは、主に下記の3点です。
- 外観検査の自動化によって高速化を実現
- 高精度の検査により品質が安定
- 外観検査の自動化で省人化を実現
それぞれのメリットについて、詳しく解説します。
外観検査の自動化によって高速化を実現
外観検査の自動化による、最もわかりやすいメリットは高速化です。外観検査の自動化は、人の手による目視検査よりも高速処理ができます。複数人で行っていた目視検査も機械検査であれば、一連の作業工程のなかで自動化されます。つまり、高速化によって検査工程に必要なスペースの節約もできるのです。
また、機械は人間のように疲労を感じません。したがって、24時間休まずに検査をし続けられ、結果的に検査工程のコスト削減に大きく貢献します。
高精度の検査により品質が安定
外観検査を自動化することで、今までは見逃していたような微細な不良も判別できるようになり、品質も安定します。
微細な異物や傷などの判別は目視検査では難しいため、画像認識が最適です。近年の画像認識は高画質の画像であっても高速処理が可能になってきました。顕微鏡レベルでなければ認識できなかったような不良も自動化によって判別できます。また、AIの発展も目覚ましく、最適なモデル学習を行なうことでより高精度な判定が可能となりました。
画像認識やAIを利用することで、目視検査のようなばらつきも抑制され、安定した製品供給が可能です。さらに目視検査のための教育が不要な点も大きなメリットでしょう。
外観検査の自動化で省人化を実現
外観検査を自動化することで省人化も可能となります。最もわかりやすいのは、複数の検査が必要な場面です。自動化により複数の検査を同時に行なえるため、省人化を実現できます。
また、外観検査を実施する際には、研修などの検査の準備も必要です。自動化によって準備にかかる手間と時間を大幅に削減できます。
人が介在する工程を削減できるため、ヒューマンエラーの削減も可能です。しかも、検査をするために必要なスキルも、作業員の間で差が生まれません。したがって、属人的な業務がなくなり、人員配置も容易となります。
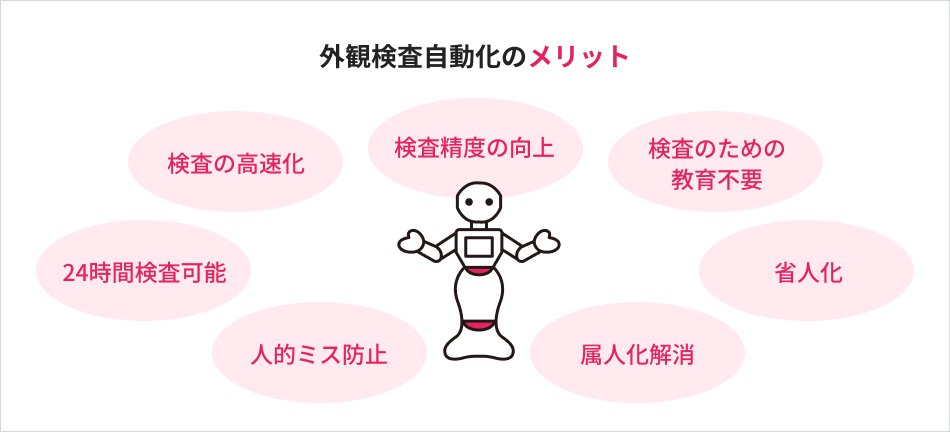
4. 外観検査の自動化による2つのデメリット
外観検査を自動化することで多くのメリットが得られますが、残念ながらメリットばかりではありません。この章では検査方法の違いによるデメリットについて考えてみましょう。
外観検査の自動化にはさまざまな検査方法があります。たとえば下記のような方法です。
- カメラを用いた外観検査
- AI外観検査
ここでは、上記2種類の検査方法で考えられる主なデメリットについて解説します。
カメラを用いた外観検査2つのデメリット
カメラを用いた外観検査には主に下記のような2つのデメリットがあります。
- 導入コストが高い
- カメラだけでなく照明の導入コストも発生する
画像検出用のカメラは供給量も増えたことから、以前よりも価格が安定しました。しかしながら、システムとして導入するにはコストがかさみます。特に高精度のシステムを導入する場合は、複数台のカメラが必要となり、さらに費用が高くなるでしょう。
また、撮像する際には照明も必要です。外観検査に使用する照明は特殊な仕様となるため、照明の導入コストも高額になりがちです。
このように、カメラを用いた外観検査は費用面でのデメリットが大きく、導入を検討する際には必要な機能とコストのバランスを考えなければなりません。
AI外観検査2つのデメリット
近年、AIが急激に進化しており、外観検査においてもAIが活用されるようになりました。しかし、現在のAIには下記のようなデメリットがあるため、残念ながら万能とはいえません。
- 人が判定できないものは正しい判断ができない
- 学習させたデータ以外の判断はできない
AI外観検査はAI自身が勝手に判断するものではなく、判断基準を学習(ディープラーニング)させて良否判定を行なうシステムです。したがって、物事が数値化できない要素は学習が困難であり、正しい判断ができません。
また、判断には学習が必要なため、学習させた条件以外の判断が難しいです。結果として正しい良否判定ができないこともあります。
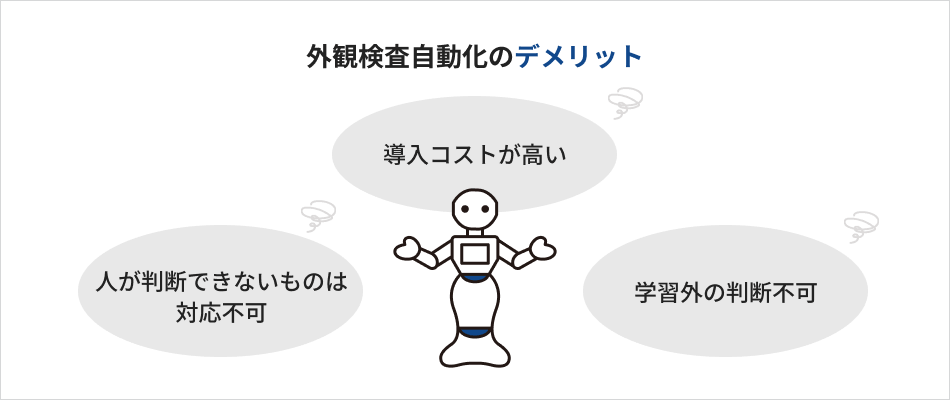
5. 外観検査の基本的な4つの手順
外観検査を実施する際には、できるかぎり効率のよい作業で、より高精度な判別が求められます。しかし、闇雲に作業を行なっていては高効率・高精度の検査を実現することは不可能です。
そこで、ここからは外観検査の基本的な手順について紹介します。効率よく、なおかつ高精度の外観検査を行う方法は、次の4つのステップです。
- 1. 準備工程
- 2. 検査工程
- 3. 結果分析工程
- 4. 改善工程
それぞれの工程について、詳しく見ていきましょう。
STEP1:準備工程
外観検査において準備工程は重要です。準備への取り組み方で検査工程全体の効率も左右されます。準備工程の具体的な内容は下記の3つです。
- 検査エリアに必要なものだけ準備する
- 検査基準を事前にチェックする
- 検査装置を正しく設定する
まずは検査エリアの清掃です。製造業では「5S」が提唱されるように、整理・整頓・清潔・清掃・しつけが重要とされます。外観検査を実施する際にも、検査エリアには必要なものだけを準備してください。
そのうえで検査基準の確認を行います。検査基準は品種や仕様によって異なることもあるため、事前確認が必要です。検査基準を確認したあとは、検査装置の設定を行ないます。検査要件をよく理解し、正しい設定を行なわなければ安定した検査品質は得られません。
STEP2:検査工程
外観検査の準備工程が完了したら、次は検査工程です。実際に製品のキズや形状などの外観を検査し、検査基準に基づいて評価を行います。
評価の結果、基準値の範囲内であれば良品と判断され、範囲外であれば不良品と判断されます。現在は多くの外観検査で画像検査が採用されており、画像から得たデータによって評価を行うのが一般的です。
検査工程で不良品と判断された場合は、あとの工程で再検査を行うか修正が行われます。そうすることで、不良品を外部に流さず品質を維持できるのです。
STEP3:結果分析工程
外観検査は検査と良否判定だけが目的ではありません。検査工程のあとには、検査によって集積したデータを分析します。データ分析によって把握できる情報は下記の2点です。
- 不良となる理由はなにか
- 検査プロセスの課題はなにか
これらの情報を元に、カメラ・照明・搬送などの検査プロセスの改善や、製造工程の生産プロセスの改善を行ないます。外観検査は検査工程が重要なことは間違いありませんが、工程だけでなく、品質の安定の視点では結果分析も大切にしてください。
STEP4:改善工程
外観検査の最後は改善工程です。データ分析の結果を元に製造ライン全体を見直し、不良品の原因を特定します。原因を特定できたら、不良を防止するための対策を立案しなければなりません。
このとき、検査プロセス全体の改善が必要な場合もあります。改善工程は、製品の品質を高いレベルで維持するための製造プロセス改善にも有効です。
また、検査装置自体の改善もしていかなければなりません。技術の進歩は目覚ましいため、最新の技術への更新も必要です。技術的な更新により、検査の精度や効率は向上します。
検査結果の信頼性を高めるためにも、改善工程に取り組みましょう。

6. 外観検査における3つの重要な品質管理機能
外観検査は製品の品質管理が大きな目的です。品質管理とは製品の外観が一定の品質を備えていることを検査・検証し、保証することを指します。
生産から販売まで一連の品質管理を行なう際には、下記3つの機能が重要です。
- 外観検査データ改ざんの防止
- QCの7つ道具の自動取込・成績表作成
- 外観検査データの一元管理
上記のどれか一つが欠けても品質管理が正常に機能しません。それでは、それぞれについてもう少し詳しく解説しましょう。
外観検査データの改ざん防止
2023年には大手自動車メーカーがデータの捏造や改ざんを行なったと大きく報じられました。データの改ざんはあってはならないことですが、多くの製造現場では外観検査におけるデータの改ざんが可能な状況にあるといえます。
例えば、下記のようなデータ管理では、簡単にデータの改ざんができます。
- 紙への記録(手書き)
- Excelへのデータ入力
上記のような管理方法では、改ざんだけではなく記入ミスや読み間違いなどが発生するかもしれません。したがって、より厳格かつ明確なデータ管理が求められるようになってきました。
企業には透明性が求められる時代です。データの改ざん防止ができるような機能を利用することが必要です。

QCの7つ道具の自動取込・成績表作成
製造現場ではQCの7つ道具が使用されます。外観検査においてもQCの7つ道具が必要です。QCの7つ道具とは、「問題点の見える化」に用いられている下記の7種類の手法を指します。
- パレート図
- 特性要因図
- グラフ
- ヒストグラム
- 散布図
- 管理図
- チェックシート
外観検査の検査データ分析にも、QCの7つ道具を使用しなければなりません。しかし、それぞれを手動で作成するのは非効率です。
このとき、外観検査のデータからQC7つ道具が自動作成できれば、品質管理・工程管理の大幅な工数削減ができます。結果的に、製品の品質が向上・安定し、市場における評価もアップするでしょう。
外観検査データをシステムで一元管理
日々の外観検査により、データは膨大となります。さらに、品質管理では検査データや解析データなどさまざまなデータを扱わなければなりません。しかし、これらのデータを個別に管理すると効率が悪くなります。
そこでおすすめしたい方法がデータの一元管理です。一元管理はさまざまな領域のデータを一箇所に集約する管理方法で、下記のようなメリットがあります。
- データ整備にかかる時間が短縮できる
- コミュニケーションの円滑化が計れる
- 見たいデータの検索が容易になる
品質管理をより円滑に進めるためには、外観検査データの一元管理機能が重要です。
7. 外観検査の自動化で品質管理業務の効率化が可能
近年は人手不足が深刻な課題となっていますが、外観検査の自動化は解決策の1つといえます。ただし、外観検査の自動化には費用面や設定面でのデメリットもあるため、理解したうえで取り入れましょう。
宇部情報システムでは、品質管理・検査データ管理の課題を解決するQC-Oneを提供しています。
検査装置を品質管理システムQC-Oneに連携することで、検査データの自動取り込みが可能です。QC-Oneとの連携は、品質管理業務効率化やデータ改ざん防止、ヒューマンエラー防止にもつながります。
また、QC-OneはQC7つ道具のうち、検査データを使ったQC道具(散布図、パレート図、ヒストグラム、管理図)の自動作成や成績表自動作成にも対応しています。外観検査の効率化を目指している方は、検査の自動化とQC-Oneの連携をぜひご検討ください。

8. 外観検査に関するよくある質問
外観検査のメリットやデメリットなどについて詳しく解説してきました。外観検査は品質管理上重要な工程であるため、正しい知識と情報を得ることが非常に重要です。
そこで、ここでは外観検査についてよくある質問に回答します。外観検査の導入や自動化を検討されている方は、ぜひ参考にしてください。
Q.外観検査を自動化するのにかかるコストは?
A:画像検査システムを導入する場合、約15万円〜導入可能です。しかし、より高度な検査項目を取り入れたい場合はオプションで追加するかたちになるので、あくまでも基準として考えるといいでしょう。
また、AI外観検査システムの場合は企業ごとに必要な製品や機器を集めて作成することが多いので、価格表記がされていないサイトが多いです。性能によって価格幅があるので、予算と性能のどちらを重視するか優先度を決めて導入するとよいです。