Column
コラム
【品質管理担当者必見】管理図とは?|工程管理でラインを安定化
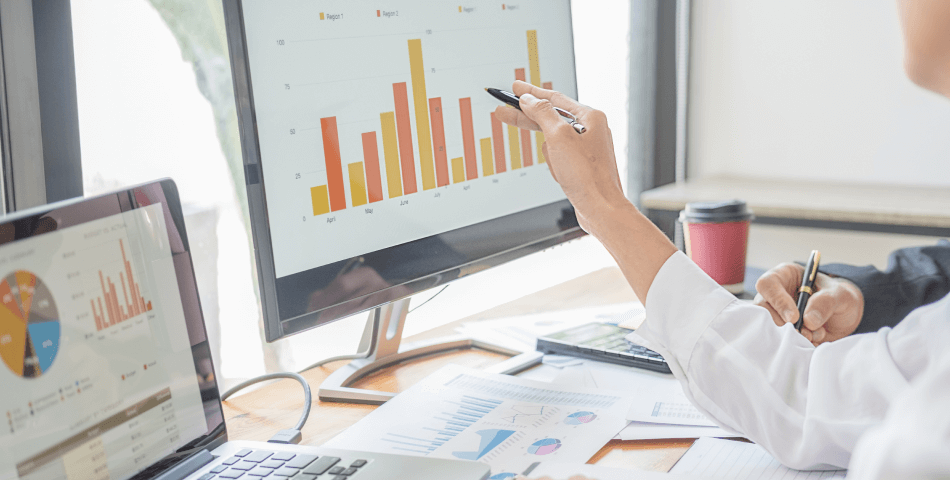
製造業で品質のばらつきを低減するには、品質管理が必須です。また、品質管理を円滑に進めるには、QC7つ道具の1つである「管理図」の作成が有効です。
この記事では、製造業の品質管理に携わる管理者の方に向けて、管理図の基礎的な知識や、具体的な事例を紹介します。品質のばらつきに悩まれている方は、ぜひ参考にしてください。
目次
1. 管理図とは
品質管理における管理図は「QC7つ道具」の1つとして知られています。
管理図は製造業の品質管理に使用されており、製造工程の安定度や、ばらつきの判断が可能です。管理図を導入することで、製造状態の特徴・傾向を可視化し、品質のばらつきについて分析・管理ができます。
さらに時間経過とともに測定されたプロセスの変数や特性をプロットし、以下の3つの指標と比較することでばらつきを可視化します。
- 1. 中心線(CL:Center Line)
プロセスの平均値を表す -
2. 上限管理限界(UCL: Upper Control Limit)
標準偏差の3倍の限界値(CL<UCL)。
平均値から標準偏差の3倍の範囲に設定される上限を表し、CLよりも常に上にある -
3. 下限管理限界(LCL: Lower Control Limit)
標準偏差の3倍の限界値(LCL<CL)。
平均値から標準偏差の3倍の範囲に設定される下限を表し、CLよりも常に下にある
基本的には、プロットされた点が許容範囲(LCL〜UCL範囲内)に収まっていれば安定していると判断可能です。さらに、プロットした点の挙動を分析することで、異常を早期発見できます。
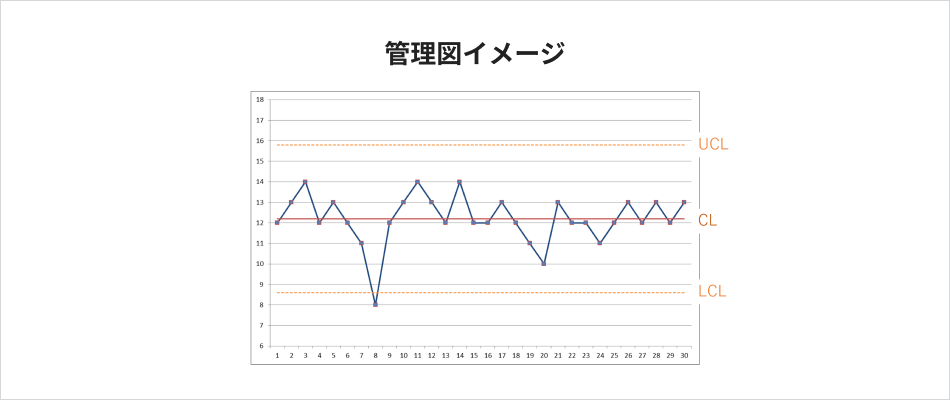
2. 管理図を使うと何ができる?
管理図にはさまざまな目的・活用方法があります。ここでは、管理図の目的を3つ紹介します。
- 工程の安定性を監視
- 異常の早期発見と根本原因の特定
- 品質改善のための意思決定
管理図はばらつきの可視化以外にも、異常の早期発見や改善策を考えるために便利なツールです。ここからは、製造現場の導入事例を含めた管理図の特徴を詳しく紹介します。
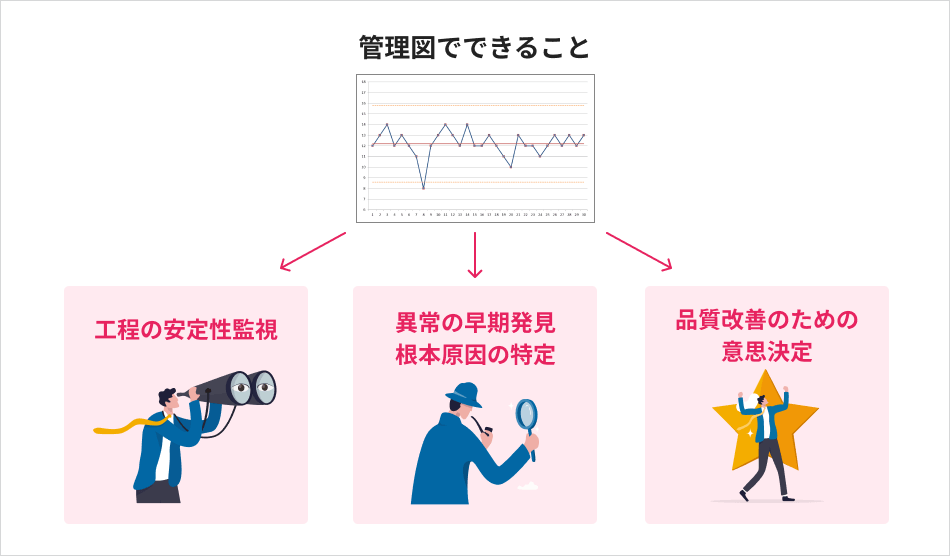
工程の安定性を監視
管理図では、製品のばらつきが監視可能です。ばらつきをリアルタイムで監視できるため、正常な状態を保持しながら製造できます。
なお管理図は、大きく「計量値管理図」と「計数値管理図」に分類されます。
区分 | 種類 | 概要 |
---|---|---|
計量値管理図 | X−R管理図 | 測定値の平均とばらつきを同時に計測できる |
X−s管理図 | 標準偏差を用いてばらつきを計測できる | |
計数値管理図 | np管理図 | 不適合品(不良品)数が分析できる |
p管理図 | 不適合品数の割合や比率が分析できる | |
c管理図 | 欠点数の割合が分析できる | |
u管理図 | 欠点率の割合が分析できる |
どの管理図も生産工程の変動や安定性を定量的に監視する有用なツールです。不良品やミスの発生を未然に防ぎたい場合は、「結果を表す計数値」よりも「結果に影響を与える計量値」を利用するとよいでしょう。
異常の早期発見と根本原因の特定
管理図を使用することで、不良品の発生を未然に防げます。また、異常なパターンが発生した場合に、問題の根本原因を特定する手がかりとなります。
異常を早期発見するためには、以下のポイントを理解して使用しましょう。
工程が安定している状態 |
---|
・プロットした点が管理限界線内にある ・プロットした点の並び方に偏りやクセがない |
範囲内に収まっていても異常となるケース |
---|
・中心線の片側に7点以上の打点が続く ・7点以上の上昇または、下降傾向にある ・データの分布に2つ以上の山がある ・限界線付近に頻繁に点がプロットされる |
異常を見つけた場合、品質管理の担当者は速やかに原因究明・対策を検討する必要があります。製造現場のリーダーと協議し、判断を仰ぎながら運転を再開すれば、高い品質を保持できます。
品質改善のための意思決定
データ分析の精度が高まれば、適切な意思決定が可能となり、材料・機械・工程などさまざまな面で変更や改善が可能です。一方でデータ分析の精度が低い場合は誤った意思決定によって、問題がより複雑化する可能性が高まります。
品質管理の現場では、管理図やパレート図などさまざまなグラフを組み合わせて使用します。各グラフにはそれぞれ異なる特性があるため、品質管理の担当者は特性を理解しておきましょう。
種類 | 特性 |
---|---|
折れ線グラフ | ・ 連続的変化を捉えるグラフ ・ 経過での変化を分析できる |
棒グラフ |
・ 棒の高さで数量データを比較するグラフ ・ 項目の大小の順番を判別できる |
円グラフ | ・ 円形状のグラフ ・ 構成比を確認できる |
これらの基本的なグラフの特性を理解したうえで、管理図やパレート図のような高度なグラフを活用することが重要です。
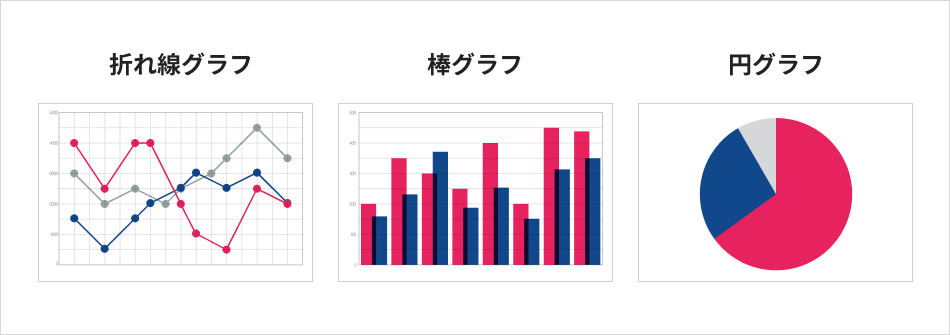
3. 管理図を含む「QC7つ道具」の基本的な使用方法
「QC7つ道具」は、日本科学技術連盟(JUSE)が提唱する統計ツールであり、高度な製造プロセスの分析を可能にします。またその簡便性から「身の回りにある問題の95%は、QC7つ道具を適切に活用すれば解決できる」といわれています。
- 「QC7つ道具」
- パレート図
- 特性要因図
- ヒストグラム
- 散布図
- 管理図
- グラフ
- チェックシート
ここからは「QC7つ道具」の詳細を解説します。それぞれの特徴と活用事例をしっかり理解しましょう。
パレート図:問題点の整理を行い優先順位を明確化
パレート図は、データを項目別に集計・分類し、多い順に並べて棒グラフと累積曲線で表現する図です。構成比の全体を把握し、集中度合いを把握することに適しています。
パレート図のメリットは、どの項目がどの程度影響を与えているのかを明確にできる点です。例えばキズや欠け、汚れなどの不良項目をパレート図で整理することにより、原因ごとに不良件数を把握でき、改善の優先順位を決定できます。
改善後もパレート図を用いれば、改善の効果・変化を視覚的に判断できます。また改善前と改善後の縦軸の目盛りを同じ値に設定することで、効果の大きさが一目で分かります。
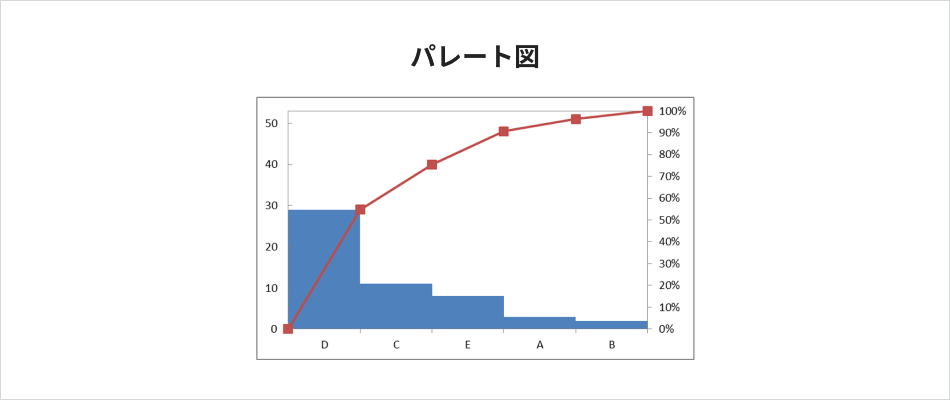
特性要因図:問題の原因を体系的に分析
特性要因図は、「特性」とそれに影響を及ぼす可能性のある「要因」との関係を表した図です。ここでいう特性とは、「結果」「問題点」「解決」を意味します。
また、魚の骨に似ていることからフィッシュボーン図とも呼ばれます。特性要因図を用いることで問題の原因を深掘りでき、結果と要因を整理するのに便利です。
特性要因図の主な利点は、問題点の整理・可視化により、ほかの方と情報を共有しやすくなる点です。現場スタッフの情報共有ツールとしても有用であり、チーム全員が同じ図を参考にすることで、認識の違いが生じず、原因究明もスムーズに進められます。
さらに特性要因図の作成過程で新たな要因に気づいたり工程を見直したりすることで、作業を効率化できるなど、さまざまなメリットが期待できます。
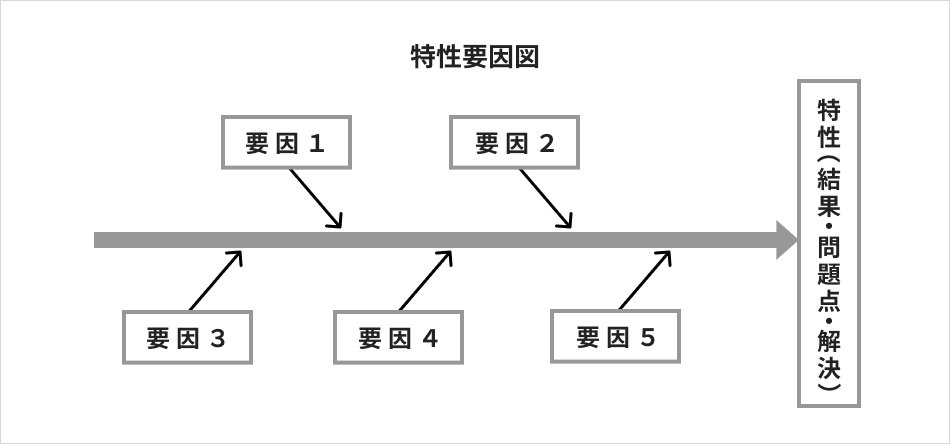
ヒストグラム:データ分布からばらつきを可視化
ヒストグラムは、横軸に階級(データが取りうる値の範囲をいくつかの区間にわけたもの)、縦軸に度数(各階級に含まれるデータ点の数)を取った縦棒グラフです。データの全体像や傾向をつかむことに優れており、データ分布の形状から製造工程の問題点の発見・分析が可能です。
ヒストグラムを作成する際は、平均値や標準偏差、最大値、最小値などの指標を活用します。また品質にばらつきが発生する原因を突き止めて、次の行動の手がかりとすることも可能です。
なお、ヒストグラムと棒グラフの主な違いはプロットされるデータの種類です。ヒストグラムが連続尺度データで使用されるのに対し、棒グラフは個々のデータで使用されるため連続性がありません。
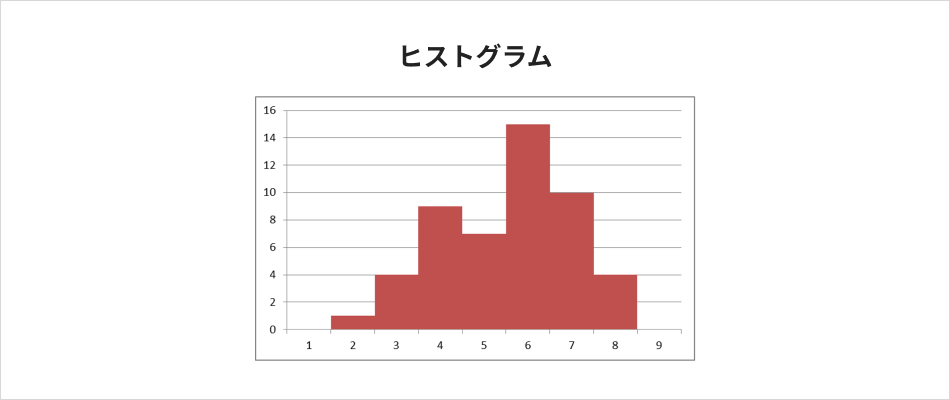
散布図:相関関係を可視化
散布図は、横軸と縦軸にそれぞれ別の数値を設定し、データを打って2つの項目の関係性を視覚的に示すグラフです。
縦軸と横軸に相関関係が見られる場合は、改善したい項目を絞り込めます。例えば、縦軸・横軸ともに増加傾向にある場合には「正の相関関係」があると判断可能です。プロットした点同士が密集している場合には、縦軸と横軸の相関関係が強いといえます。
ただし、散布図はあくまで要素同士の相関関係を明確にできるものであり、両項目の因果関係までは示せません。そのため、どちらの項目が問題の原因となっているかは別途調査が必要です。
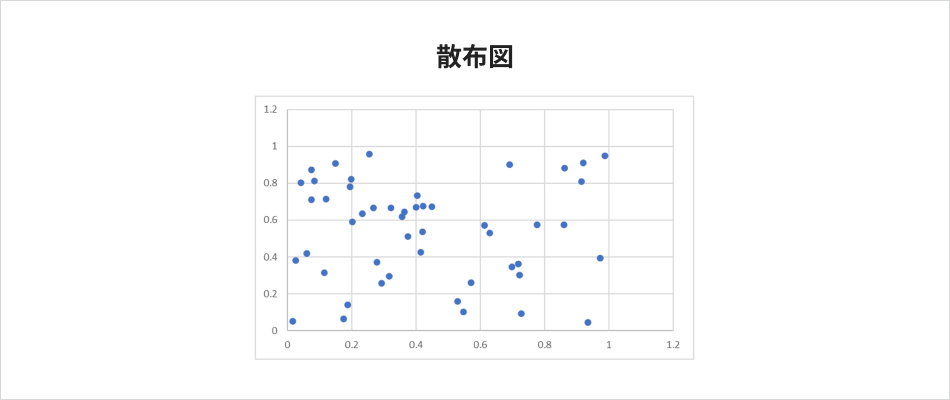
管理図:品質や工程の管理状態を可視化
管理図は、製品の品質が安定した状態にあるのかを図で表したものです。上方管理限界線、または下方管理限界線内にプロットされていても、異常の傾向を把握できます。異常パターンを見分けるために、日本産業規格(JIS)では以下のようにルールづけされています。
- 異常判定ルール(新JIS基準)
- 1. ゾーンAを超えた一つの点
- 2. 中心線の片側上のゾーンCの中で又はそれを超えて、一列になった9点
- 3. 一列になって上下方向に増加又は減少する6点
- 4. 一列になって交互に上下する14点
- 5. 中心線の片側上のゾーンAの中で又はそれを超えて、一列になった三つのうちの二つの点
- 6. 中心線の片側上のゾーンBの中で又はそれを超えて、一列になった五つのうちの四つの点
- 7. 中心線の上下のゾーンCの中で一列になった15点
- 8. 中心線の両側上で一列になった八つの点で、ゾーンCに点はない
引用:JISZ9020-2:2016 管理図-第2部:シューハート管理図
※新JIS管理図ではUCL-CL、CL-LCLを3分割し、領域A,B,Cとして区分しています。(領域A.B,Cに関する図)
グラフ:数値の比較や変化を可視化
グラフは、データの特徴を簡単に把握できるツールです。グラフには棒グラフや折れ線グラフ、円グラフ、帯グラフ、レーダーチャートなどさまざまな種類があります。
一般的にグラフは、以下の項目を可視化するのに適しています。
- 量の大きさ
- 割合
- 時系列の変化
- 項目間のバランス
グラフの活用により数値だけではわからない情報を発見でき、データに説得力をもたせることが可能です。また、目的にあったグラフを選択することが重要です。
チェックシート:点検項目の抜け漏れを防止
チェックシートは、事前に設定した項目を点検する表です。業務内容や手順を項目化し確認できます。簡単に作業の漏れを防止できるため、利便性が高いQCツールです。
品質管理の現場では、「不良項目別チェックシート」や「点検用チェックシート」などが使用されています。不良品の数と内訳などを整理しながら確認できるため、数字ではわからない製造工程の実状を把握可能です。
チェックシートを制作する際は、以下のポイントを意識しましょう。
- 記入間違いを減らすために、チェック欄を大きめに設定する
- エクセルで制作する際には、仕様が変更されないように保護をする
- 重要な項目はダブルチェックする
目的やデータの性質などに応じて、最適な形式に工夫することが大切です。
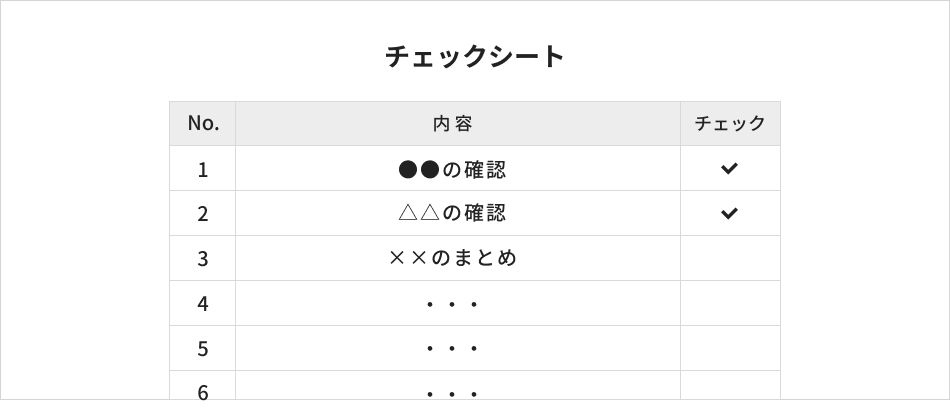
4. 【応用編】6つの管理図を使い分ける
管理図は、1924年にアメリカの統計学者シューハート氏によって発明されました。現在では以下の管理図が多く活用されています。
- X-R管理図
- X-s管理図
- p管理図
- np管理図
- u管理図
- c管理図
管理図ごとに分析・監視できる項目が異なります。それぞれの特徴を理解し、自社の製造工程にあわせた管理図を用いましょう。
X-R管理図
製造プロセスの状況を、広範囲にわたって詳細に把握するために役立ちます。寸法、硬さ、感応性、経過時間、温度、電気抵抗、電流、引っ張り強度など、多岐にわたる品質属性を数値で監視し管理可能です。
X-R管理図を作成する際は、X管理図とR管理図をそれぞれ作成し、上下に配置して比較します。
- X管理図:測定値の平均をグラフ化
- R管理図:群ごとのばらつきをグラフ化
なおX-R管理図のサンプリング数は8つ程度までが望ましいとされており、サンプリング数が10以上になる場合はX-s管理図を用いることが推奨されます。
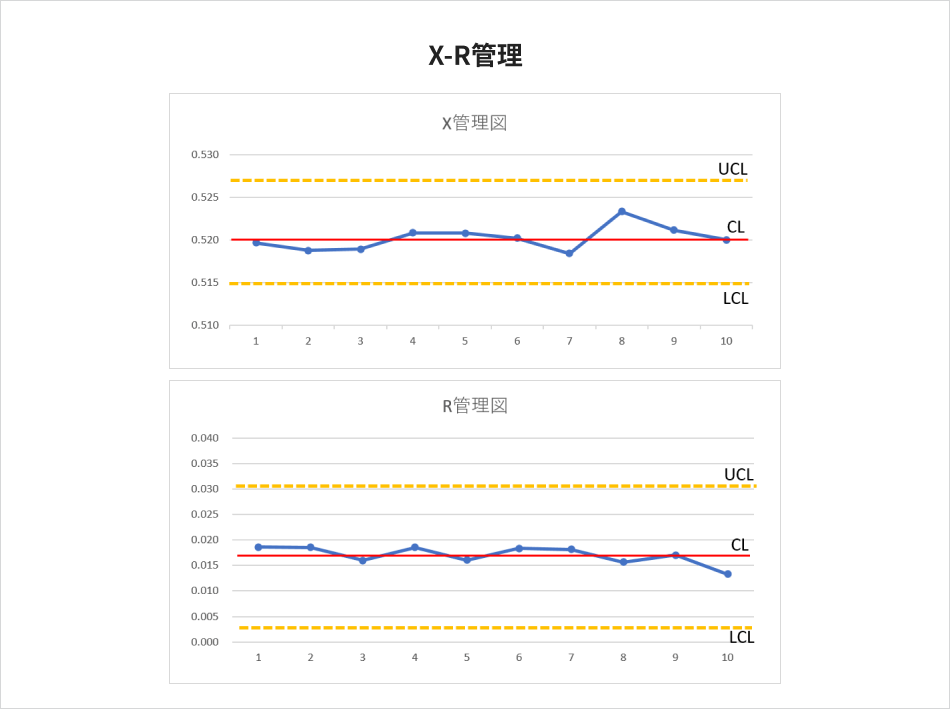
X-s管理図
プロセスの平均値(X)とそのばらつき(標準偏差s)を監視するために使用される管理図で、ばらつきの挙動を把握しやすいのが特徴です。以下2種類のグラフを作成し、異常状態を計測します。
- X管理図:測定値の平均をグラフ化
- s管理図:群ごとのばらつきをグラフ化(標準偏差を用いてグラフ化)
X-s管理図は標準偏差で表現するため、10以上のサンプルサイズが必要なときに用いられ、全体の変動を把握できます。
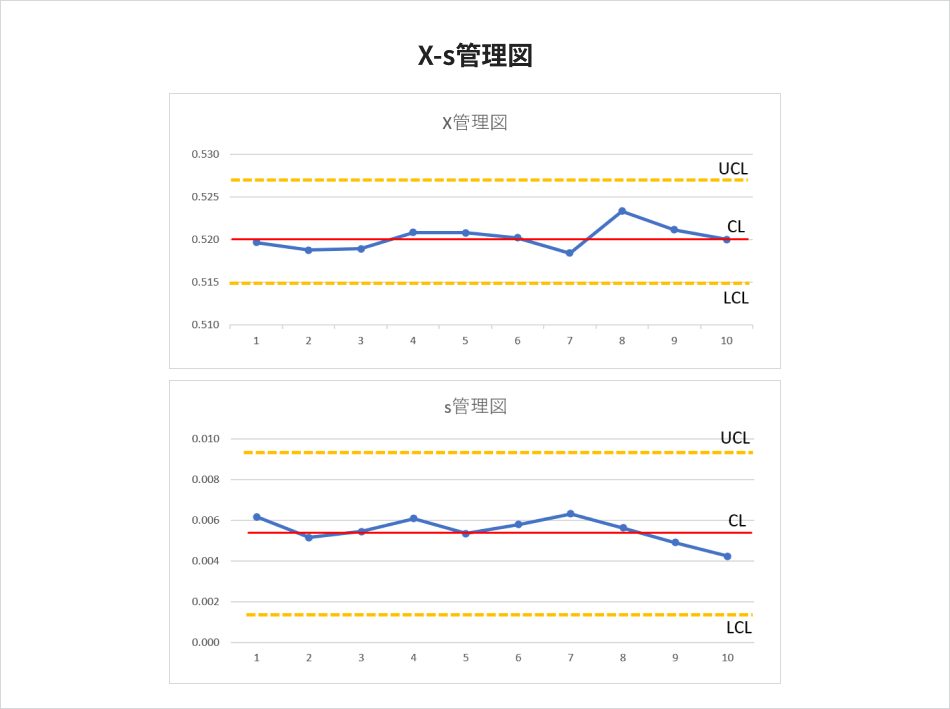
p管理図
不適合品率pを管理するグラフです。製造プロセスの品質管理において、検査されたアイテム数に対する欠陥品の割合を分析するために使用されます。
欠陥品の割合を追跡できるため、異なるサイズの検査ロットにも柔軟に適用可能です。例えば単純な欠陥数での管理が難しい状況では、各ロットの欠陥率を計算し、これを制御限界線とともに図示して利用します。
p管理図は時間経過にともなうプロセスの安定性を監視することで、プロセスのパフォーマンスに影響を与える潜在的な問題の特定が可能です。さらに原因分析を通じてこれらの問題に対処し、必要な改善措置を講じられるでしょう。
np管理図
サンプルデータ数を示すnと、不適合品率pをかけ合わせた不適合品数npから算出したグラフです。二項分布がベースとなっており「製品の中から不良品がいくつ発生したか」という不良数の管理に適しています。
u管理図
異なるサイズ単位で発生する不良品数を追跡し、工程の品質管理に役立てるグラフです。各単位における不良品の平均数(u)、その平均を中心とした管理線(CL)、そして品質の変動を示す上下の限界線(UCLとLCL)を用いて、製造プロセスの一貫性と制御を評価します。
さらに管理限界を超える異常値を検出し、その数と詳細を把握できます。
c管理図
一定の面積や長さ、またはサンプルサイズをもつ項目の不適合数・欠点数cを、品質管理を行う目的でグラフ化したものです。例えばプリント基板上のキズや修理箇所の数を追跡する際に有効です。この場合、欠点を見いだす範囲が一定である必要があります。
5. 管理図の作り方・使用方法
管理図は一般原因(システム内の自然なばらつき)と特殊原因(非常に異常または非予測的な変動)を区別するための有効な方法です。ここからはX-R管理図の作成方法について紹介します。
ステップ | 種類 | 概要 |
---|---|---|
STEP1 | データ収集 | 管理項目となっている製品のデータを収集する |
STEP2 | サンプルの平均値と範囲の算出 | 各サンプル群の平均値(X)と、最大値と最小値の差(範囲R)を計算する |
STEP3 | 最大値と最小値の差の算出 | 最大値と最小値を調べ、ばらつき(R)を計算し差を求める |
STEP4 | 総平均値・ばらつきの算出 | Xの平均値とRの平均値を計算する |
STEP5 | CL・UCL・LCLの計算 | CL・UCL・LCLをそれぞれ計算す |
STEP6 | グラフ化 | X管理図とR管理図を上下に並べて、CL・UCL・LCLの線を引く |
STEP7 | 管理線の延長 | 管理線を延長して今後の製造工程を管理する |
STEP8 | プロセスのモニタリング | 製造中に定期的にXとRを計算、管理図にプロットし、異常な動きがないかを監視する |
STEP9 | 定期的な管理線の見直し | 製造プロセスにおけるばらつきを監視し、適宜見直す |
上記フローに従って作業し、管理図を作成しましょう。
6. 工程の安定性を監視するには品質管理システムの導入がおすすめ!
工程の安定性を監視するには「品質管理の知識」が不可欠です。しかし複雑な工程であればあるほどデータ収集は難しく、解析も非常に困難な作業となります。
「QC-One」は検査データをデジタル化することで、品質管理DXを実現できるシステムです。データ解析機能を活用して品質管理データを自動的に解析し、製造工程の問題や原因を見える化することで、様々な領域に影響を与えます。また、SPCルールに基づいて品質管理データが基準値から外れると、指定した担当者に自動通知されます。これにより、高度な品質管理DXを実現可能です。
品質管理の強化をお考えのご担当者様は、下記よりお問い合わせください。