コラム
リードタイム短縮で競争力UP!リードタイムを短縮するメリットと方法とは?
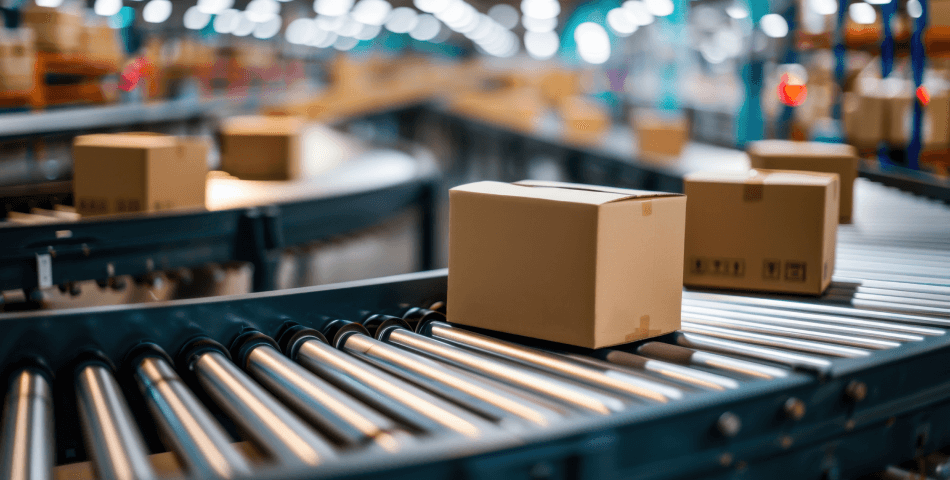
まさに今製造現場では、商品ニーズの変化に伴ってリードタイム短縮が喫緊の課題となっています。「リードタイム短縮をしたいが、なかなか結果が出ない」と、お悩みの方は多いのではないでしょうか。生産計画に特化したシステム・生産スケジューラは、需要変動にあわせた生産計画を迅速に立案し共有できるなど、リードタイム短縮に効果的です。これにより、仕掛在庫を削減でき、キャッシュフロー改善などの効果も得られるため、製造業において重要な課題といえます。
今回は、リードタイムを短縮すべきプロセスや有効な施策を紹介します。また、生産スケジューラがリードタイム短縮にどう効果を発揮するのかについても、詳しくまとめました。リードタイム短縮でお悩みの生産管理部門の皆さまは、ぜひご覧ください。
目次
1. 「リードタイム」とは?
リードタイムとは、製品やサービスの開発・生産・提供など、特定のプロセスやタスクの完了までにかかる時間のことです。製造現場においては、注文を受けてから製品が完成し、顧客に納品するまでの時間を示します。リードタイムは、製造現場におけるQCD(品質・価格・納期)を左右し、商品競争力を維持・強化する重要な指標です。
また、リードタイムは下記4つの要素の影響を受けます。
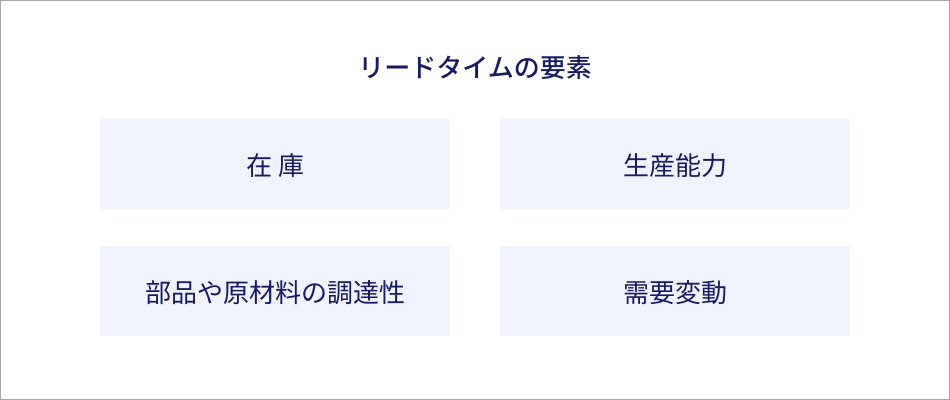
- 在庫:サプライチェーン全体で使用可能な在庫数
- 生産能力:製造設備や人員などのリソース
- 部品や原材料の調達性:サプライヤーからの柔軟な供給
- 需要変動:経済や季節性、商品競争力による需要の変化
それぞれの要素が複合的に影響しあい、リードタイムが決まります。
2. リードタイム短縮が必要な理由
近年、製造現場ではさまざまな理由からリードタイムの短縮が求められています。
インターネットやSNSの普及に伴い、消費者ニーズの変化が激しくなっているため、ニーズの移り変わりが早くなっています。そのため、スピーディな製造が求められています。また、ECサイトでの取引が増えるなかで、商品の迅速な納品がECビジネスの成功要因となっています。
このように、商品の「多品種少量化」「短寿命化」「短納期化」が進むなかで、リードタイムの短縮が求められているのです。
3. リードタイムを短縮すべきプロセス
リードタイムには、下記の4つのリードタイムが存在します。
- 開発リードタイム
- 調達リードタイム
- 生産リードタイム
- 物流リードタイム
それぞれのリードタイムは、さらに細分化できます。細分化すると、役割分担や責任所在、時間がかかっている箇所の特定が可能です。待ち時間が発生している工程を特定できれば、ピンポイントで対策できるため、リードタイム短縮につながります。
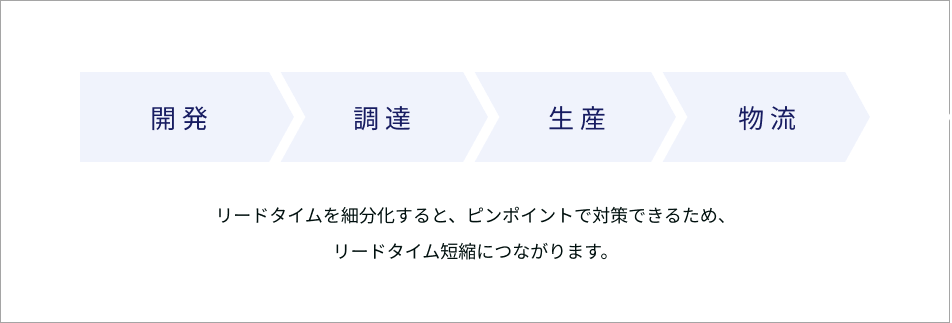
ここでは、4つのリードタイムに含まれる工程や短縮すべき理由を解説します。
開発
開発でのリードタイムとは、製品の企画から製品・工程設計までにかかる時間のことです。開発リードタイムには、詳細設計と生産準備が含まれます。
詳細設計では、設計・試作・実験により製品の詳細を決めます。性能や価格は、競合との差別化要素です。生産準備では、生産ラインの構築を行い、品質や生産性を確保します。
開発リードタイムは、商品リリースを行い、顧客へ提供する時期を左右します。そのため、短寿命化する商品への対策としては、開発リードタイムの短縮が重要です。
調達
調達でのリードタイムとは、原材料の発注から納品までにかかる時間のことです。納品・受入・検査の工程が含まれます。
納品工程は原材料の発注から納品、受入工程は納品から受入、検査工程は受入れ後の検査を実施するプロセスです。生産計画や在庫管理における原材料の発注計画で、調達リードタイムが使用されます。
調達リードタイムの短縮は部品や原材料を短期間で補充できるため、短納期化した需要への対応力が向上します。
生産
生産でのリードタイムとは、製造開始から完成までの時間のことです。製造の工程に応じて、加工・組立・検査などが含まれます。さらに各工程は、作業時間や待ち時間、段替え時間など、時間を構成する要素にも細分化できます。
待ち時間や段替え時間の長期化は、仕掛在庫を増加させ、在庫管理負担の増加や倉庫スペースの圧迫につながります。
生産リードタイムの短縮によって、生産リソースを有効に活用できるようになり、需要変動に対して柔軟な対応ができるようになります。
物流
物流でのリードタイムは、製品の出荷を指示してから顧客へ納品されるまでの時間です。出荷工程と輸送工程が含まれます。
出荷工程は出荷指示からピッキング・検品・梱包等から出荷まで、輸送工程は出荷から納品までのプロセスです。
顧客への迅速な納品につながるため、物流リードタイムの短縮は重要です。多品種少量生産のニーズ増加に対しては、作業の効率化や人的ミスを削減する新たな取り組みが必要となり、出荷場のレイアウト見直しや、一括読み取りが可能なハンディターミナルの導入が有効です。
4. リードタイム短縮の効果
リードタイムの短縮により得られる効果として、下記の4つがあげられます。
- 需要変動対応力の強化
- 顧客満足度の向上
- 在庫の削減
- キャッシュフローの改善
リードタイム短縮は、生産工程の効率化だけではなく、企業価値の向上にもつながります。これから、それぞれの効果を具体的に見ていきましょう。
需要変動対応力の強化
生産リードタイムの短縮によって、設備や人員のリソースをより効率的に活用できるようになるため、需要増に対する生産対応力を強化できます。
また調達リードタイムの短縮は、迅速な原材料の補充ですぐに生産可能な状態にできます。原材料の在庫を気にせず顧客納期に合わせて生産計画を組めるため、需要変動のブレを吸収する効果も期待できるでしょう。
需要が変動した際は、設備や人員のリソースを該当商品の生産に引き当てられます。
在庫の削減
1. 仕掛在庫の削減
仕掛在庫は、まとめ生産、工程間の能力差などの理由により、物が滞留することで、増加します。仕掛在庫が増加すると、工場の生産スペースを圧迫するなどの悪影響が出ます。
逆に、この滞留を防げば、仕掛在庫を減らすことができますが、滞留を防ぐには、工程間の待ち時間を減らして生産リードタイムを削減することが必要です。
例えば、加工工程完了から、組立工程開始まで、待ち時間が30日空いていたところ、組立開始の5日前に加工完了するよう工程を同期させて計画するだけで、仕掛在庫の保有期間が30日から5日短縮されます。先に作りすぎている工程については、後工程に合わせた生産計画にするだけで、改善ができます。
2. 安全在庫の削減
見込み生産で、製品在庫を持つ業種の場合、欠品を防ぐために、安全在庫数を設定し、その在庫数を維持するように生産計画を立てます。この安全在庫数は一般的に以下の式で求められます。
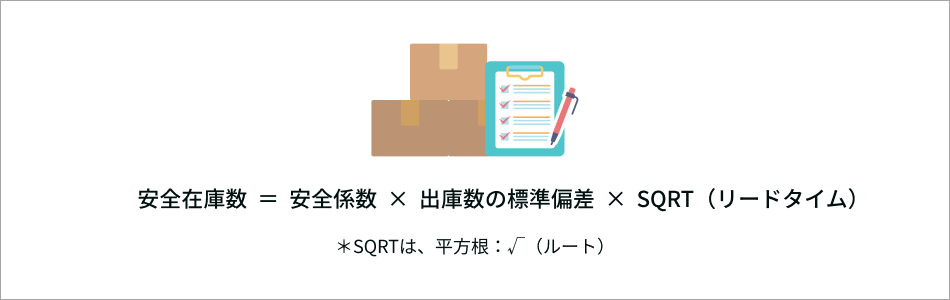
上記の式から分かる通り、リードタイムを短縮すれば、安全在庫数は少なくなります。
例えば、安全係数:1.65、出庫数の標準偏差:10、リードタイム:10日とした場合、安全在庫数は、53となります。リードタイムを10日から5日して計算すると、37となり、3割減らすことができます。
つまりリードタイムを短縮すると、無駄な在庫が減り、また、無駄な生産設備の占有を減らすことにつながります。
顧客満足度の向上
納期は、製造業で重要視されているQCD(品質・価格・納期)の構成要素です。商品の「短納期化」が進むマーケットでは、商品競争力の向上において納期は差別化ポイントになります。
顧客も短納期に対応するために、需要変動に迅速かつ柔軟に対応可能なベンダーを優遇するでしょう。
リードタイム短縮により商品の短納期化が可能となり、顧客の要望を満たします。結果として顧客満足度と信頼度が高まり、ベンダーとしての地位を向上させ、長期的な取引関係の構築が可能となります。
キャッシュフローの改善
製品を作るために、着手時にお金を借りて、必要な物を仕入れ、製造、販売を行って、初めて現金化されます。リードタイムが短縮されることで、お金を借りてから、実際に現金が入るまでの期間が、短くなります。
5. リードタイム短縮に有効な施策
リードタイム短縮において有効な施策は、下記の通りです。
- 製造現場の実態の把握
- 設計仕様の共通化
- 半製品の汎用化
- 小ロット化
- 段取り時間の短縮
- 計画手法の改善
リードタイム短縮は部門横断の施策が重要になります。以下では各施策の具体的な内容を解説します。
製造現場の実態把握
製造現場の実態を把握し、省ける無駄がないかを確認することが重要です。
工程ごとに、待ち時間、段取り替え時間、製造時間をウォッチし、その時間が妥当かどうかを確認します。具体的には、整理整頓ができていないことが原因で、物を探すのに時間がかかっており。その些細な時間が、月単位、年単位で見た場合に大きなロスになっていないかを把握していきます。
また、ボトルネック工程となる設備が明確な場合、その設備が工場の生産能力となるため、基本的には稼働率が高くなるはずです。ボトルネック設備の稼働率を確認し、稼働が下がる時がある場合は、滞留しなくてもよい工程で滞留されている可能性があります。
現場の実態を把握し、課題を見つけることが先決です。
設計仕様の共通化
新商品開発の設計工程では、設計仕様を共通化しましょう。実施済みの設計と検証を省けるため、開発リードタイムが短縮できます。
設計仕様を共通化するには、設計プロセスの手順や方法論を文書に落とし込みながら、組織全体で進めるとよいでしょう。具体的には、設計書のフォーマットや、用語・定義の統一などです。情報が整理できれば、組織内の情報伝達がスピーディーになり、設計仕様の共通化がスムーズに進みます。
半製品の汎用化
途中工程までの半製品を、複数の製品として使えるよう汎用化を行い、汎用化された半製品を見込みで生産して在庫化しておくことで、受注から出荷までのリードタイムを短縮することができます。
下図のように、3つの製品の1工程目、2工程目を、半製品として在庫化しておくことで、受注してから、仕上加工の1工程のみを行って出荷することができるようになります。
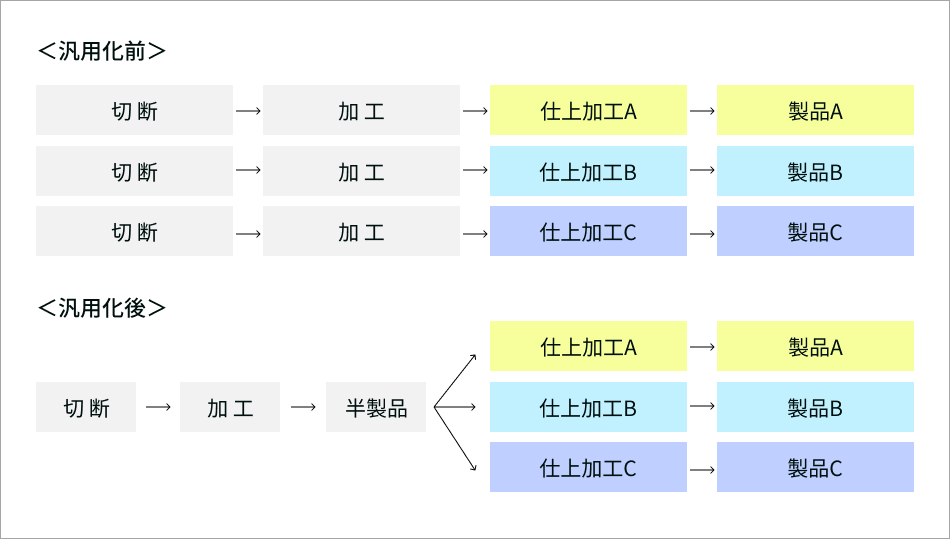
小ロット化
受注が小ロットでも、生産の都合上大ロットで製造することがあります。大ロットの場合、各工程の設備の占有時間も増えます。その間、他の製品は作れないため、待ち時間が多く発生します。
逆に、小ロット化すると、待ち時間が減り、必要な時期に、必要量のみを生産するため、リードタイム短縮につながります。
※小ロット化すると当然段取り回数が増えます。1回の段取り時間が長くかかる工程では、逆効果になる場合があります。
運搬時間
工程間の運搬時間短縮の具体例を説明します。
- 工程順と設備のレイアウトを合わせることで、工程間の移動の無駄を削減します。
- 部材や副資材などの在庫は、使用する設備の近くに配置することで、払い出しにかかる時間を削減します。
- 運搬待ちで滞留する場合は、運搬便の数を増やし、運搬待ちの時間を削減します。
段取り時間の削減
-
整理・整頓
段取り替え作業のなかで、治具や交換部品、前製品の片付けがあります。それぞれ「探す」という時間が含まれますので、整理整頓を徹底し、探す時間を短縮します。 -
外段取り化
設備を停止させる内段取りから、設備を止めずに作業を進められる外段取りに、移行させることで、設備の停止時間を短縮できます。段取り作業を細分化し、外段取り化できる作業を、先に実施するよう作業順を見直すことで改善できます。
計画手法の改善
-
計画時間メッシュの細分化(日単位→時分単位)
基幹システムのMPR機能から作業指示を出されている企業などでは、日単位で計画を立案されていることが多いです。全工程完了に5日程度で完了する場合でも、10工程あり、1日1工程で計算しているため、10日間かかる計画としているケースはないでしょうか。
計画のメッシュを日単位から、時分単位にすれば、1工程:10時~12時、2工程:13時~16時という計画が可能で、これだけでリードタイム短縮につながることがあります。
日単位からいきなり時分単位の生産計画に変更することが大変であれば、1日をAM/PMの二つに分けるだけでも改善につながります。 -
組立着手に合わせた加工の製造計画(バックワード計画)
仕掛在庫削減の所でも説明しましたが、前工程と後工程の間が空きすぎる場合があります。
下図の1段目のように部品加工については、部材があれば着手できるため、早く着手しすぎて、組立開始までの間、2ヵ月も空いております。2段目のように、計画を組立開始の直前に部品加工の計画し、製造指示を出すことで、仕掛品の在庫の削減が実現できます。
6. リードタイム短縮の成功事例を紹介!
リードタイム短縮に成功した機器製造メーカーA社の事例を紹介します。
A社では、製造現場の負荷が把握できないまま、生産計画をExcelで管理していました。そのため、製造納期が不明確で、残業や手待ちなど負荷のバラつきが発生する課題を抱えていました。また、生産拠点間の情報が連携されておらず、生産調整に時間が掛かっていたのです。
そこで課題解決のために、生産計画スケジューラ「FLEXSCHE」を導入しました。
導入の結果、工場内負荷を見える化し、負荷を考慮した生産計画が立案され、生産可能数と納期が明確になりました。また、生産拠点間の情報が一元化され、生産調整などの生産計画業務の効率化ができました。
生産リードタイムも短縮し、仕掛在庫を25%削減することができました。さらに、生産人員の適正化で、直接作業員を4.8%省人化できました。
生産計画の見える化を実現!FLEXSCHE導入事例をご紹介
https://www.uis-inf.co.jp/flexsche/case/case04.html
スマートファクトリーを実現する
生産スケジューラ「FLEXSCHE」